By Dale Nelson, Roof Hugger, LLC
Retrofitting of older metal building roofs continues to grow in popularity with good reason.
• Rehab of older buildings is much less expensive than building new.
• There is little or no disruption of ongoing operations within the building.
• Thermal upgrades are easily accomplished on top of the old roof.
• Hardening an older building to meet or exceed today’s newer more stringent building codes.
• Upgrades from old thru‐fastened roofs to new standing seam roofs is simple.
This popularity has given rise to many questions about what can and cannot be done over an old metal roof. The following are the questions we most commonly hear from owners, contractors and designers considering retrofitting an existing metal roofed building:
1. YOU CAN ONLY RETROFIT 12” O.C. SCREW DOWN, R‐PANEL TYPE ROOFS. ‐ Not correct, metal panels of all types and rib spacings can be retrofitted. Screw‐down, standing seam and corrugated.
2. IF YOU HAVE AN EXISTING SCREW DOWN ROOF YOU HAVE TO PUT BACK ANOTHER SCREW‐DOWN ROOF. - No, you can upgrade to a new standing seam roof that has few if any exposed fasteners by using the proper retrofit framing system. You can of course install
a new screw‐down roof if you wish but remember screw‐down roofs have approximately 0.8 fasteners per sq. ft. thus a 10,000 sq. ft. building will have at least 8,000 fastener penetrations, a common source of leaks. Standing seam roofing is also the
perfect platform for attaching photovoltaic (PV) panels. The PV panels can be attached to the standing seam roof without penetrating the roof and most importantly this new metal roof will have a 40- to 60‐year life...much longer than the PV panels,
unlike all other roofing systems that will need replacing during the life of the PV panels at significant expense.
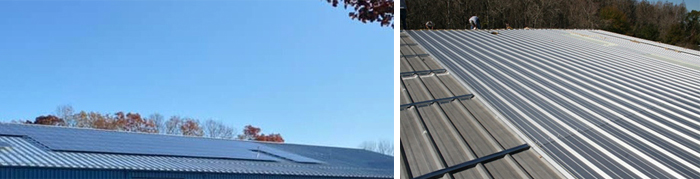 |
3. CAN I REMOVE AND REPLACE MY EXISTING ROOF PANELS WITH A LIKE KIND PANEL? ‐ Yes, most building officials allow you to remove and replace an old screw down, corrugated or standing seam roof with “equal to original” panels. The question
is why would you? Removing the old roof will expose the building interior to the weather, disrupt ongoing operations, there will be falling debris, new insulation will be required, the old panels and insulation will have to be disposed of and you
will likely still not comply with the latest, more stringent building code requirements for wind and/or snow.
4. I JUST WANT TO REMOVE MY OLD SCREW-DOWN ROOF AND INSTALL A NEW STANDING SEAM ROOF. - This is possible but could end up being a very expensive option. Removing the old roof will also remove the diaphragm strength the old roof provides. This can
make the entire building structurally unstable without significant re‐bracing of the existing purlin system. Retrofitting can enhance the diaphragm strength and is the perfect platform for the new standing seam metal roof.
5. MY ROOF HAS BEEN COATED OR HAD FOAM SPRAY APPLIED TO IT, CAN IT BE RETROFITTED? ‐ It absolutely can be retrofitted, even roofs that have foam spray on them. Coatings are almost never a problem unless the coating has trapped moisture between
the panel and the coating, causing severe corrosion of the existing panels and purlins. Foam coating is a bit more difficult but the entire roof does not have to be scraped clean, only a 2” wide strip directly above the purlin lines. The retrofit
framing will be designed to be taller than the depth of the foam so not to interfere with the new roof.
6. FOR CONDENSATION DO I HAVE TO INSULATE OR VENTILATE UNDER THE NEW ROOF? - Most design professionals will advise to always ventilate a cavity unless it is completely filled with insulation. Retrofitting is the perfect time to increase the R‐values
of the roof system. I would suggest filling the cavity with raw un‐faced fiberglass insulation. It’s easy to do and fairly inexpensive. Rigid insulation systems are also easily done. You can choose not to insulate but you must ventilate the
cavity. Keep in mind if you don’t insulate and the new roof is standing seam you may experience something called “panel rumble”. This is when, in certain wind conditions, the pan section of a standing seam panel will flutter and
hit the sub‐framing below, making a rumbling noise. Insulating or installing foam blocking will separate the framing from the sheeting, preventing that metal‐on‐metal rumble.
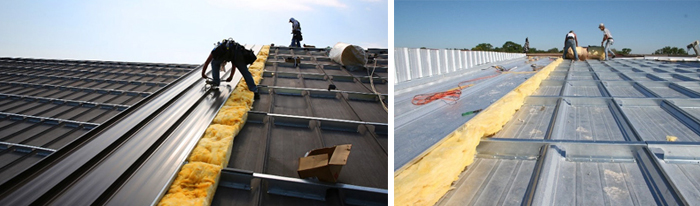 |
7. WHAT ABOUT THE EXTRA WEIGHT OF THE NEW FRAMING AND METAL ROOFING? - The typical metal-over-metal retrofit will add approximately 1.70 – 2.50 lbs./sq. ft. in total. That breaks down on average like this: retrofit framing 0.5 – 1.0
lbs./sq. ft., the new panels 0.8 – 1.25 lbs./sq. ft. and insulation 0.15‐0.25 lbs./sq. ft. The International Existing Building Code allows the addition of a second roof over the existing roof up to 3.0 lbs./sq. ft. without a full structural
analysis. In many cases, retrofit framing systems like the Roof Hugger System have actually been shown to add capacity to the existing roof purlins in excess of the additional weight of the retrofit. Every building is unique so check with your engineer
or roof system provider.
8. COATING IS JUST AS GOOD AND LESS EXPENSIVE TOO – RIGHT? - Well, it will be less expensive but did you know coatings are not waterproofing? They are commonly sold that way but coatings are only intended to extend the life of the existing
roof surface they are covering. We are talking about a 4‐6 mil spray finish on top of a metal roof. Waterproofing is done with what is call “liquid applied roofing” a 40‐80 mil system that is a significantly more expensive and complex
system. Neither will do anything to bring the building up to the current codes and frequently they cover up serious structural issues. They often trap moisture between the old metal roof and coating, causing corrosion and shortening the useful life
of the existing roof.
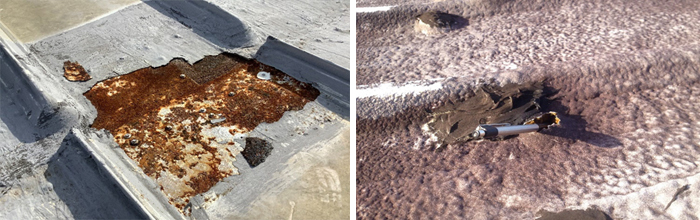 |
When it is time to reroof that old metal roof, look seriously at the many options available for retrofitting your roof. Don’t spend a significant amount of money for a 2‐ to 10‐year patch that will have annual maintenance and repairs, when you can
have a 40‐ to 60‐year life roof that is code compliant, highly insulated and available with weathertightness warranties.