By Jeff Alexander, The Valspar Corporation
Exterior architectural coatings serve many purposes, including the protection of a building’s structure from degradation and corrosion. It’s important to note that many times architectural coatings are applied onto a structure’s exterior metal panels as the first step in the metal building product process – before the panels are formed and well before they’re shipped to the construction site. This means that building owners and contractors need to think about the threats these metal panels, and consequently the coatings that protect them, could endure at the very beginning of a project.
Backed By Demand
Market research firm IRL found in a recent study that a major performance trend in architecture is the demand for increased corrosion-resistance in architectural coatings. Clients are expecting architectural coatings to last as long as possible before repairs and maintenance are needed. Similarly, building owners are especially interested in this, as longer lasting architectural coatings directly translate to reductions in building upkeep costs.
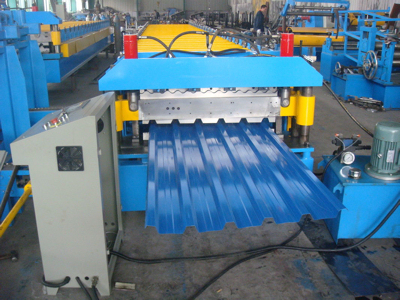 |
| In order to pass the durability test, coatings need to withstand the bending and shaping that metal panels undergo during fabrication, in addition to environmental factors, like hail damage, after the panels are installed. |
Protection
The most reliable coatings on the market are formulated to resist different kinds of abrasion that can occur before and during the installation process. These types of abrasions include marring, scratching, etching and what happens frequently during the inevitable wear and tear at the manufacturing facilities, on the road and at the job sites.
In order to pass the durability test, coatings need to withstand the bending and shaping that metal panels undergo during fabrication, in addition to environmental factors, like hail damage, after the panels are installed.
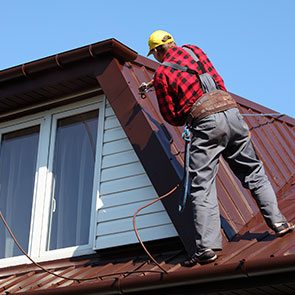 |
Architectural coatings must look good, but they must also be tough enough to resist marring and scuffing during handling and installation. | |
Testing
The best way to ensure the level of durability needed for most projects is to continuously test, formulate and research new and existing architectural coatings. There are various testing methods that coating manufacturers have used to examine the level of durability possessed by a coating. Commonly, manufacturers study how two surfaces react when they come into contact with each other as a way to evaluate the comparative difference in coating wear resistance characteristics.
Many tests analyze the level of damage a product can withstand. Some companies go as far as staging potential scenarios and have research teams recreate the repetitive, sliding, surface-on-surface friction that panels are subjected to as they are fabricated, shipped and installed.
Lastly, testing to failure is a great way to seek out innovation and learn where improvement is needed. Some companies test for gloss retention, chalking, fading, blistering, cracking and flaking. They push their products as far as they can go to truly see the limits when it comes to durability.
Ultimately, architectural coatings should be providing superior flexibility, formability and color consistency during the manufacturing process and superb protection against harsh outdoor elements and abrasion once they’ve been applied to panels. Through rigorous and continuous testing, coating manufacturers will learn just how durable their products are, which is critical when formulating new materials as well as improving on old formulas.
From color retention, scratch resistance and cost reductions, there are many reasons why durability is at the top of the list for needed qualities in architectural coatings. It’s time now more than ever for coating manufacturers to examine their products and continue to test and ensure they are providing the industry with a durable architectural coating that delivers from beginning to end.