All Weather's OneDek™ Roof System Saves Time And Money On Low-Slope Projects
By Ted Johnson, All Weather Insulated Panels
In Europe, the use of insulated metal panels (IMPs) comprises about 50 percent of building projects in the commercial-industrial category. In North America, IMPs, though growing, remain in the minority – about one in 10 projects use them. More telling, however, is that the vast majority of IMPs in Europe are for roof applications. In America, it’s walls.
That discrepancy is attributable to the fact that energy and raw material costs are considerably higher in Europe. Since the roof poses the greatest threat to the security of a building’s thermal envelope, IMPs are often considered an economical necessity in Europe.
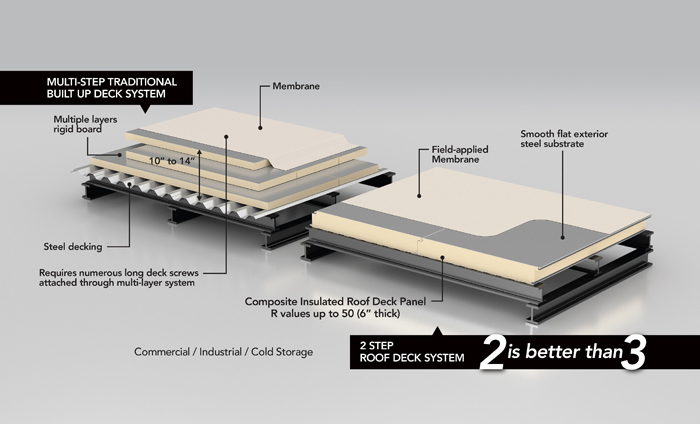 |
All Weather Insulated Panels' new OneDek™ product is designed specifically for large, low-slope projects. |
As long-time IMP innovators in the cold storage industry, the R&D staff at All Weather Insulated Panels has developed a revolutionary roof system for large low-slope projects that provides long-term energy efficiency while bringing significant savings during installation. Called OneDek™, this roof system uniquely meets or exceeds all of the physical properties of a traditional insulated roof assembly over steel decking. We do it by factory forming the insulation and steel deck components into a single composite called RD1.
When overlaid with a field-installed single-ply membrane, RDI becomes a simple and superior two-step roof assembly, the “OneDek™ system.” We believe in the OneDek™ system so much that an industry exclusive, “top-to-bottom” 20-year warranty is available – a first in the cold storage industry.
Our roll-formed tongue-and-groove joinery enables long length panels (up to 6-inches thick, R value 50) to slide together and be mechanically attached to the roof’s secondary structural supports, with fastening patterns depending on specific project requirements. Then the white PVC or TPO membrane is either installed mechanically onto the 22ga RD1 deck surface or adhered (or self-adhered) to the factory-primed surface.
Up To $1 Million A Week
The two-step installation of OneDek™ eliminates the costly, time-consuming second step of adding and then securing the rigid board insulation to the steel deck. On a 100,000- square-foot R-50 roof typically found on cold storage and warehouse buildings, up to 20,000 drill holes are needed to secure the insulation.
On projects like that, it’s common to expect a cost of $1 million a week for labor, insurance, ancillary materials and equipment rentals. OneDek™ requires less than a third of the fasteners, cutting weeks out of installation time and large chunks out of equipment rental and labor costs. Reducing a time-consuming, repetitive task that cuts two weeks roof installation means eye-opening savings.
Another savings: shipping. The RD1 panels are a “one-time” load-and-ship product. Traditional built-up roofs require trucks to carry the B deck then more trucks to carry the fiber board insulation. The RD1 panels in the OneDek™ system arrive ready for installation.
Savings by using OneDek™ don’t stop there, however:
- The OneDek™ roof system has been tested for fire, wind uplift, thermal integrity, deflection and diaphragm shear resistance, the latter exceeding typical performance levels of 22ga 1½”-inch deep B deck.
- The RD1 deck component of the OneDek™ roof system can be installed in inclement weather unlike traditional “built-up” roof assemblies, whose fiberboard cannot be applied in rain.
- Work crews gain added safety in knowing they can walk on the panels without fear of damaging the rigid insulation or the substrate. That security can lead to fewer accidents, which can cut down on a company’s insurance costs.
- The USDA acceptable factory applied-white paint finish on the interior of OneDek™ RD1 panels eliminates post painting, inhibits corrosion and lowers the interior lighting requirement compared to standard galvanized steel finish.
More than anything, we feel OneDek™ reduces the concern all building owners and project managers have at the start of any project. Knowing ahead of time that a project can be “dried in” in less time, at less expense and still perform to the highest standards required for cold storage and food processing applications might be No. 1 benefit of OneDek™. This revolutionary product will change the way cold storage roofs are built.
For more information about OneDek™, email sales@awipanels.com or visit www.awipanels.com.
About All Weather Insulated Panels
Headquartered in Vacaville, CA, All Weather Insulated Panels (AWIP) is an innovator in the
design, construction and advancement of insulated metal wall, roof and
deck solutions. They are strategically positioned to meet the growing
energy, environmental and economic challenges
facing the North American building industry. For more information, visit www.awipanels.com.