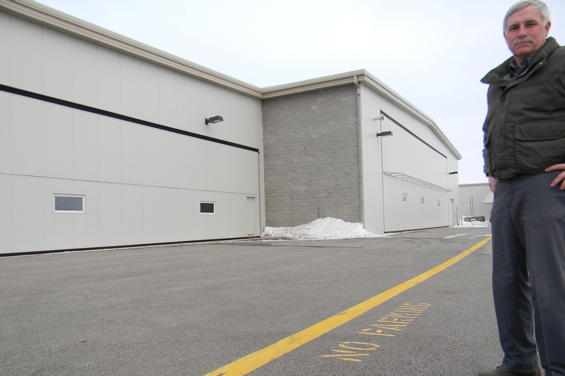
Marty Kiehm of Kiehm Construction Inc. stands before one of his company's many insulated metal panel projects.
By Dick Hagen
Back in 1980, Marty Kiehm, 20 years old at the time, built his first structure. It was a 70’ x 100’ hangar in Delavan, MN, that featured a 48’ bifold door.
Though not yet a licensed pilot, aviation blood was already trickling through Kiehm’s veins. His dad was an aerial applicator so ‘flight talk’ was a routine part of family conversations. Following in his Dad’s footsteps, however,
was not.
Because he was a gifted student/athlete at Delavan High School, Kiehm gained an appointment to the U.S. Air Force Academy in Colorado Springs, CO. But a military career lost its excitement after his first year at the Academy. Construction was his
ambition and if his love for flying could match up with a business career, so much the better. So Kiehm said ‘good bye’ to the Air Force and ‘hello’ to Augsburg College in Minneapolis where he graduated in 1983 with a business
degree.
Today, Kiehm Construction Inc. of Lakeville, MN employees 35 people at their office/warehouse/manufacturing facility at the Lakeville Air Park, and Marty Kiehm flies a twin-engine Cessna 340 with pressurized cab.
“This is the plane I use to visit clients, move clients to jobs, even travel prospective clients to view our work,” Kiehm said. “I probably fly more than most pilots because my plane fits so well with our expanding business. I have
a number of things going on across the country and I need to move from point A to point B. So aviation is truly a business necessity for me.”
And while his plane is essential for getting from point A to point B, it’s his high regard for composite foam panel construction that has his business now spreading across the country.
“We’ve found a niche and have figured out how to prospect the product,” he explained. “I think it’s a far superior product to typical metal construction. Because we’ve learned how to work with the product, we often
complete a project ahead of schedule and below the original bid price.
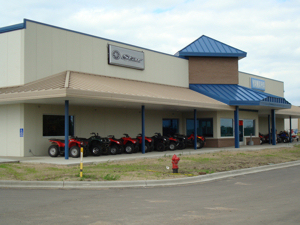
| |
| |
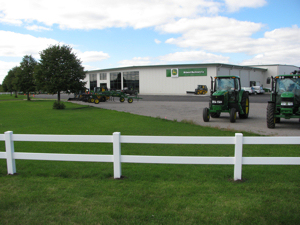
| |
Kiehm Construction's projects range from sales and service dealerships to self-storage facilities both large and small. The company also designs and builds aviation-related structures. Click images to enlarge.
| |
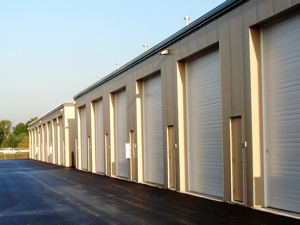
| |
| |
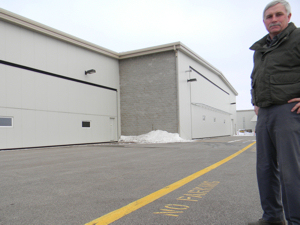
| |
Insulated metal wall panels are utilized frequently by Kiehm Construction, as are doors by Schweiss Doors,
when the project calls for large doors. Click images to enlarge.
| |
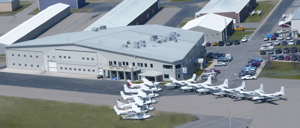
| |
| |
“This is an excellent example of a product selling itself,” he continued. “We’re now selling to a national account that started with a 12,000 sq. ft. building in Shakopee, barely 20 miles from our office. They loved their building.
Because this firm handles a product needing lots of vertical space, we’re building these structures with 24’ composite foam panel sidewalls. “They’ve asked us to follow them around the country. Right now we’re doing
a building for them just outside of Washington DC. Our next project with them is in Connecticut. They’re enthused about the attractive, finished look of their buildings. As a contractor/builder we appreciate the convenience of working with
such a product.”
Kiehm credits his employees for the company being able to simultaneously manage several projects at once but credits the use of insulated metal panels for speeding them to completion.
Retracing the recent construction economy, Kiehm indicated 2008 was his company’s top revenue year so far. “2010 was a good year also but not quite measuring up to 2008. But this economy is constantly changing and we’ve had to change
accordingly. We’re moving into a couple of other construction areas. We’re migrating into these other areas because money is in different places right now.”
Keeping an open mind about new business opportunities, he sees energy and agriculture as two industries with lots of growth, lots of new money. North Dakota’s rapidly expanding oil drilling industry just might be one of those new opportunities
for Kiehm Construction.
“And we’re seeing inquiries from the Ag market for a ‘better building’ than the traditional pole structure which has dominated agriculture for several years. Both farmers and rural builders see the advantages of steel and the
convenience of clear spans, especially as farm equipment keeps getting bigger and bigger.”
Geothermal heated/cooled structures with in-floor heating systems and insulated composite foam walls for both modern farm shops and commercial farm equipment dealers are now frequently showing up on the ‘construction bid’ agenda of Kiehm
Construction. “We’ve done millions of square feet of in-floor heat. It’s a phenomenal product with the only question being how you are going to fuel it: waste oil, propane, natural gas, or the full route of geothermal,”
he said. “Geothermal is much more expensive but the payback is there; it’s just a matter of how long do you want to wait for it.”
On the topic of insulation products, Kiehm cautions that there’s more to insulation than just ‘R’ values. “Fiberglass has a place because it’s an economical product. Air infiltration is a big factor. The closed-cell stops
air infiltration and that’s what makes the composite insulated panel such a great product. It has all the advantages of precast: great insulator, impervious to water, air infiltration is practically zilch. However the panels do not have
the ‘impact durability’ of precast.”
As the product gets more popular, there are more sources. Metl-Span,
Kingspan Insulated Metal Panels and
MBCI are ones Kiehm regularly turns to, plus there are now
compatible products to make the finished building more architecturally attractive such as stone coatings, special stucco sidings, etc. Staying current on new products and new ideas is something the contractor always tries to do.
“Trade shows, reading trade journals, and of course sales reps calling on us are the tricks to being abreast of what’s new,” Kiehm said. METALCON is one
of the best trade shows on earth for guys like us who specialize in metal buildings,” he points out. He also said they pay attention to the Concrete Expo each year because that show also introduces new concepts, new products. “And
with the new LEED programs coming forth, there’s just a lot of information that you need to pay attention to.”
Like most contractors, Kiehm follows closely what’s happening in the energy world. He thinks solar and other energy sources will start playing a larger role in the construction industry. “People tend to think of solar as more suited for
southern areas because the ‘sun season’ is considerably longer. But solar actually works better in our northern climates; in the south, solar tends to overheat. It’s a great product. Our challenge is figuring an easy and convenient
way to keep the snow off in the winter season.’” He also raises the question of how do you make solar panels visually attractive from street level.
How does he handle ‘new traffic’ asking about energy issues, multi-functional doors, etc? “When you see demand, you start to inquire. You have to educate yourself so you can share good information with your people.”
Reflecting on Kiehm Construction history he said his firm has now done upwards of 30 hangars at various airports across the state, from Brainerd to Red Wing plus virtually every ‘reliever airfield in the Twin Cities areas. Plus they’re
into high-end self-storage buildings of 50,000 to 100,000 sq. ft. featuring drive-through accessibility and climate controlled environments. Earlier in his career he built a few Fire Halls. He never ventured into pole barn construction much preferring
the structural integrity of steel.
At the Lakeville Air Park, Kiehm Construction recently built two hangars, both featuring composite insulated panels and both equipped with Schweiss bifold
doors. The 70’ x 60’ hangar is a 24/7 operation for a Med-I-Vac helicopter service. It features a 50’ x 16’ Schweiss bifold. The bigger 100’ x 80’ hangar operates with an 80’ x 20’ Schweiss bifold.
His affinity for Schweiss doors partly stems from the obvious of seeing Schweiss doors dominating hangars across Minnesota and the nation. “But also Mike Schweiss has been very helpful, very positive on any of our inquiries. He and his crew
readily offer suggestions on how to overcome a particular door issue on any construction job. We’ve done retrofit jobs getting doors on buildings that structurally were not capable of carrying the door but the Schweiss crew shows us how
to adapt their doors to any building.
“They build quality,” he states. “I’ve also noticed that Schweiss manufacturing is always looking for ways to improve their product. They’ve taken a very simple product, i.e., the bifold door, and tweaked it, improved
it functionally. Their lift-strap device is a remarkable engineering coup. And now Schweiss gives you a choice, the ‘Strap’ bifold or the Hydro Power hydraulic door. I’m more a fan of the bifold, perhaps because we’ve done
so many.
“I’ve suggested to Mike that he consider this composite insulated panel material for his doors. It’s the perfect solution for insulating a door without having to work around the framing structure of the door. Composite panel installed
on the exterior gives you a full R25 or R32, depending on the thickness you put on. Schweiss is an innovative outfit so they’ll likely give this a try,” he said.