Superior Wind Resistance For Retrofit Roof Applications
By Mark James, RetroSpec LLC
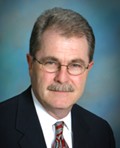 | |
Mark James is President of RetroSpec, LLC. He has been an active contributor to the growth of the retrofit concept in the metal construction marketplace since 1986. |  |
With building code changes over the last decade or so, retrofitting existing buildings in coastal areas with metal roofs have become even more difficult and complex. The changes in code have dramatically increased the load requirements in the edges and corners of a roof - a challenge not easily met by most standing seam panels on the 5’ purlin spacing common in older buildings.
There is an easy solution to these conditions, but before this is announced, allow the following to explain the basics of roof design today and how it relates to retrofitting metal existing buildings.
The vast majority of metal roof manufacturers have tested their products to determine the ultimate strength. This testing reveals that most systems will require panel clip spacing of 2’-6” or less to be adequate in these high load areas.
As mentioned earlier, most metal buildings constructed prior to 1995 have purlins spaced at 5‘-0”. This is a major obstacle when planning to remove the old metal roof and install a new metal roof directly over the existing purlins or even in a metal-over-metal application where the existing roof remains and a structural sub-purlin system is used between the old and new roofs. The extreme pressures in higher wind areas, the edge and corner zones mean the new panel must have clips placed between the existing purlins by adding additional purlins or creating an above old roof, structural “grid” for a metal-over-metal installation.
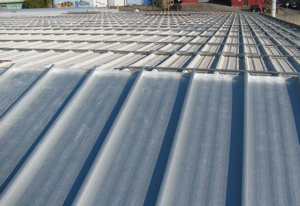 | |
The Seventh Street Wharf warehouse in New Orleans, LA (shown above) was one of the buildings battered by Hurricane Katrina in 2005. Problems with the building's R panel metal roof were eventually remedied by installing Architectural Building Components' 238T standing seam metal roof system right over the top. Facilitating the metal-over-metal retrofit was Roof Hugger's factory-notched retrofit sub-purlin. Click image to enlarge. |  |
There are three recognized standards of performance testing for metal roof systems. The one considered “THE” standard in the metal construction industry is the ASTM E-1592 or the American Society of Testing Materials’ Standard Test Method for Structural Performance of Sheet Metal Roof and Siding Systems by Uniform Static Air Pressure Difference. These tests attempt to simulate actual conditions by applying air pressure to the underside of the roofing assembly in a laboratory controlled test chamber, approximately 10’ x 20’. Tests are conducted by applying pressure until panel failure at varying purlin spacing occur. The failure points are recorded and converted into PSF results.
UL testing, is a pass/fail test in a 10’ x 10’ vacuum chamber with the maximum applied force equal to -105 psf.
Factory Mutual FM Standard 4471 is the other nationally accepted test criteria. While this test is very similar to the E-1592, FM projects will have greater pressures to be satisfied. It is typically only used when projects are required to have a FM certification for insurance purposes. Most metal manufacturers have FM tested their metal roofs in order to participate in this segment of the metal roofing market and many can design in accordance to FM criteria, when the certification is not required.
All test values are expressed in pounds per square foot (PSF) and are typically then divided by 2 as a factor of safety. Thus a panel achieving -130 psf in the E1592 chamber would have a useable -65 psf. These results are then used in engineering calculations to determine the panel clip spacing specific to any given retrofit roofing project.
To illustrate the differences in requirements, an existing metal building with 5’-0” purlin spacing located in the central U.S. will more than likely require to be designed to a 90 MPH wind speed, but that same building along the Gulf Coast will require a 130 MPH or greater depending on occupancy type and proximity to the coastline. A sample project in a 90 MPH area will result in design pressures of -19 PSF in the interior zone of the roof, -31 PSF at the edge zones and -47 PSF in the corners. In order to satisfy these pressures with a 2.00 safety factor applied, the new metal roof would need to have achieved a minimum of 94 PSF (2 X 47) in its E-1592 testing with 5’-0” purlin/panel clip spacing. For the coastal 130 MPH building however, the pressures are -39, -66 and -99 PSF respectively.
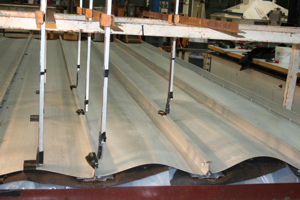 |
The problem is that most 16-inch wide vertical rib standing seam metal roofs will test out between 80 and 90 PSF ultimate with 24-gauge base material. Switching to 22-gauge instead will increase capacity by up to 25%, but usually not enough to satisfy extreme wind loads with a purlin spacing of 5’-0”. Trapezoidal standing seam systems are usually weaker. With the 2.00 safety factor applied on the 24-gauge system, the maximum allowed panel design pressure is up to 40 or 45 PSF (80 or 90 ÷ 2). So the central U.S. 90-MPH building design will require additional grid type sub-framing (see photo) in the corners and the coastal building 130 MPH at both the edge and corner zones. Depending on the size of the re-roofing project, this can cause a major cost difference in the sub-framing package and/or a more expensive heavier-gauge panel system and result in a non-competitive system or more simply put: You losing the bid.
McElroy Metal’s newest panel system, the 238T-Rib standing seam roof system, coupled with Roof Hugger’s factory-notched retrofit sub-purlins is the unsurpassed best choice for high wind prone areas. Why? The 238T has been tested over 5’ o.c. Roof Hugger sub-purlin assemblies with phenomenal results for both E-1592 and FM. As a point of interest, the 238T was developed by Architectural Building Components (ABC) of Houston, TX which is now a member of the McElroy Metal family of companies.
E-1592 testing of the 18" 22-gauge 238T with its continuous clip design achieved 200 PSF pressures at 5’-0” clip spacing. This test was conducted over a standard Roof Hugger, but when the test was run using the new patent pending “Gusseted” Hugger, the results were 250 PSF. What does this mean to you? The McElroy 238T over the Huggers has a useable 100 PSF or 125 PSF (200 or 250 ÷ 2) respectfully. For FM certified projects, the 238T is the only Roof Hugger retrofit metal roof assembly that has been tested and received FM 1-75 and a whopping FM 1-195 certifications. McElroy and Roof Hugger are continuing their E-1592 gallery of testing of the 238T, with plans to test other gauges and panel widths.
Also, as a point of interest, the 238T roof is the only system tested that has caused the Roof Hugger sub-purlin system to fail before the panel or its clip.
To summarize, if you have a project in a code regulated high wind load area, you now have a solution with a complete engineered systems package offered by Roof Hugger and McElroy Metal.
For more about this dynamic Metal-over-Metal retrofit solution, contact McElroy Metal, Inc. by visiting www.mcelroymetal.com or calling 800-950-6537; or Roof Hugger, Inc. at www.roofhugger.com or 800-771-1711.