SAF Marks 70th Anniversary As Anodizing Pioneer
SAF Historical Timeline |
1946 – One of the first two anodizing lines to open in the US, Southern Aluminum Finishing Co. is founded by Marvin McClatchey to meet post WWII building boom in ATL and throughout the SE. A new process at the time, anodizing proves to be a tough, durable, attractive coating option for aluminum. SAF today offers all of the preferred anodizing applications, including: Mechanical, Chemical (cleaned, etched), Protective/Decorative, Architectural Class I, II Anodic Anodized Finish options for customer-supplied aluminum sheets, extrusions, parts. 1950 – The Korean war created an aluminum shortage and SAF was invited to accumulate scrap aluminum for Alcoa in return for a valuable flat sheet allocation. Customers include industrial glazing contractors with projects that include commercial building store fronts and curtain walls. 1954 – Workers enlisted to help rebuild. No jobs lost. Fully operational again in 6 weeks. 1956 – Cutting, shearing, brake metal fabrication services enable SAF to become a One-Stop-Shop for aluminum, fabricating & anodizing – the result from SAF purchase of an aluminum awning manufacturer with fading product demand (air conditioning). 1957 – Marvin’s oldest son & first second generation family member employee, Reynolds McClatchey, begins work as Assistant Chemist in 1961, retires decades later as VP Engineering and Inventory. Over the next two decades John, James, Penn join the family business, employ their unique talents in chemical engineering, philosophy, business education and computer science to build the business to top C-level executive positions. 1968 – In the back of a building housing the SAF aluminum anodizing line SAF begins applying PVDF coatings to customer aluminum, including PPG’s Duranar®. 1969 – SAF Catalog becomes an instant customer hit. Used as a go-to resource for customer information and easy ordering. The catalog is augmented in 1995 by a popular, free SAF Aluminum Extrusion & Sheet Poster for an even easier industry reference hung on a wall. 1972 – Charlotte, NC plant receives numerous awards for waste treatment and environmentally friendly processing. 1978 – Commissions 20,000 sq ft, state of the art facility for PVDF coatings applications. Establishes SAF among the first architectural fabricators in the US with an in-house aluminum paint line. 1990 – SAF pioneers the application of portable color matching instruments for architectural anodizing, where color is critical. Opens doors to new commercial construction customers & projects. 1990 – Introduces metal commercial roof edge products: Designer Series Commercial Gutter Systems, Cornice Mouldings, and the first truly adjustable plastic coping, EP Coping. 1994 – Enables SAF to produce both toll coated and anodized aluminum coil products. Offers SAF sheet customers substantial cost-savings on quantity aluminum sheet purchases. SAF is one of 5 continuous coil anodizers in North America. 1995 – SAF is an early adopter of Internet technology for improving customer information and service. Online customer services continue to evolve to include online ordering and order tracking by the year 2000. 1996 – GA Governor Zell Miller declares Nov. 1, 1996 Southern Aluminum Finishing Day at SAF Atlanta plant to honor SAF role in contributing to the commercial growth of Atlanta, Georgia and the region. 1998 – Awarded to SAF for its significant reductions in air emissions, waste water, hazardous & solid waste. Affirms SAF commitment to pollution prevention in a traditionally “dirty” industry. 2002 – Chemical Engineer and anodizing innovator Marvin McClatchey (b. 1916 – d. 2002) and founder of SAF, one of only two anodizing lines in the country in 1946. Son, John McClatchey, continues as SAF CEO. 2003 – 78,000 square foot facility houses state-of-the-art metal fabricating with CNC equipment, in addition to SAF Perimeter Systems commercial gutter, cornice, coping and related systems manufacturing. 2003 – A first in the industry, customers are quick to respond to SAF’s unique turnaround services. To cement customer loyalty and win market share, SAF inaugurates a series of Fast turnaround services from 1 day to 3 days, and includes select Fabricating, Painting, Anodizing services, in addition to aluminum sheet & extrusions from stock. Free shipping on all orders over 100 lbs. also boosts sales and establishes SAF as a cost-saving and efficient resource. Positions SAF as a fast, reliable resource for aluminum and finishing. Pre-recession 2008 SAF reports record sales of $32MM. 2004 – SAF engineered (fabricated metal) product line expands with introduction of custom Column Covers in square, elliptical, and conical shapes, and choice of extruded aluminum attachment options. 2006 – To boost aluminum finishing speed & quality SAF installs a 20,000+ square feet conveyor run paint line. Under one roof SAF can send newly made parts directly to the paint line, lowering costs, improving customer order turn-around time while eliminating packing costs & freight damage. 2007 – Initially opens as a western US base for aluminum extrusion & sheet distribution center with limited fabrication. Expands to become a full mirror capability of SAF GA distribution, aluminum finishing, and fabrication facility by 2013. 2007 – SAF offers engineered products for the commercial building market beginning with the SAF RainScreen panel system, an affordable, dry joint, rain-screen system for effectively handling exterior moisture. Panel choices include ACM (Aluminum Composite Material), Painted or Anodized Aluminum. SAF begins a program to add at least one new panel product per year to become a leading panel manufacturer, fuels a new era of SAF innovation. Select RainScreen panel products meet High Velocity Hurricane Zone (HVHZ) requirements in 2015. 2009 – SAF CAD Design Dept. adds BIM objects to integrate architectural project specification details for panels and column covers. 2010 – National poll of metal buyers by industry-leading trade publication leads to U S Glass bestowing SAF its Preferred Metal Supplier Award. 2011 – Offers directional sanding, also called ‘brushed’ aluminum finishing option. Proves popular for a host of architectural and engineered product applications. 2011 – Designer Series extruded aluminum Cornice Mouldings provide decorative, precision joints, exceptionally crisp lines, and more refined detail than formed versions. Designer Series Pediment, Entablature and Column System is the first to feature mix-and-match extruded aluminum components in a variety of finishes. Designer Series products feature easy installation, unique concealed gussets & wall plates. In an industry first, in 2014 SAF Perimeter Systems adds custom extruded aluminum arches and radius corners to complete the SAF Perimeter Systems Designer line, eliminating a major obstacle for builders. 2012 – Offers a full line of extruded aluminum panel extrusions commonly used to hang, join and secure rain-screen panels for curtainwall applications. For use with SAF or other panel materials. Supports customers with contractor architectural panel fabrication and installation training classes.
In December of 2012 SAF ships their first anodized aluminum out of the SAF West, Redding, CA anodizing line. Gives SAF West functional parity with the east providing the same robust fabrication, finishing & distribution capabilities, and coast-to-coast customer service advantages. 2012 – Jim and Penn McClatchey adopt a co-CEO model to replace John McClatchey who retires as CEO. 2014 – SAF Press-Loc® Aluminum Gravel Stop & Coping system passes ANSI/SPRI ES-1 Wind Design standard test, ensures highest performance in commercial grade low-slope roof edge system. 2014 – Award acknowledges fluorocarbon powder coatings from SAF paint line that features a zero-discharge pretreatment system. SAF’s AAMA 2605 Duranar® powder coatings have the same performance as liquid Kynar. 2015 – SAF opens Salem, Oregon branch office to support NW business development. SAF employment nationwide reaches 300. 2015 – Acoustical grade thermoplastic application on SAF Column Covers and Panels can dampen acoustic and mechanical resonance noise up to 75% in buildings. 2015 – SAF SMACNA Series Gutters become available with heavy gage aluminum, making them ideal for commercial, industrial & high end residential building projects. Select Designer & Industrial Series Gutter Systems tested to ANSI/SPRI GD-1 Standard for Low-Slope Roofs. 2016 – SAF West commissions an aluminum cut-to-length (CTL) Aluminum Coil line that includes a state of the art Herr Voss 6-high corrective leveler for high tolerance applications. 2016 – Receives Grant to Grow Exports from Atlanta Metro Export Plan for its pro-active international efforts to expand distribution of anodized aluminum sheet, aluminum extrusions, fabricated painted, and anodized aluminum cladding for the commercial construction industry. 2016 – SAF Insulated Spandrel Pans for LEED Certified building cladding systems designed to be an energy saving component used in opaque glazing areas of the exterior envelope of the building. 2016 – SAF wins the Redding, CA Chamber of Commerce 2015 Business of the Year Award.
|
|
SAF (Southern Aluminum Finishing Co.), headquartered in Atlanta, GA, marks its 70th anniversary this fall. At its founding in 1946, SAF was one of only two anodizing lines in the country. Founder Marvin McClatchey was a chemical engineer and pioneer in anodizing for architectural applications. Still in the family, SAF is currently led by second generation brothers and Co-CEOs, Penn McClatchey and Jim McClatchey.
Early customers included commercial glazing contractors working to meet pressing demands for store front and curtain wall projects in the post WWII building boom. Since then SAF’s customer base has expanded internationally to include Construction Specifiers, Design-Build Contractors, Commercial Construction
Subcontractors, Alternative Energy Product Manufacturers, Product Engineers, Automotive Suppliers along with Fabricators and Manufacturers in many other industries. A common thread is evident in a review of company milestones: a business acumen always directed toward providing products with more customer value and better quality that ship on time.
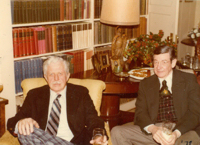 |
Founder Marvin McClatchey with his first cousin Homer McClatchey in 1978. Homer served as SAF's Controller for more than twenty years. |
In 1950 during the Korean war and an aluminum shortage, Alcoa invited SAF to accumulate scrap aluminum in return for a valuable flat sheet allocation. Soon after, SAF added aluminum sheet & extrusion distribution to its anodizing finishing services.
SAF follows a growth plan to invest in resources whenever and wherever a strategic customer benefit can be identified to reduce logistical costs, time, and potential for shipping damage. In 1956 SAF added metal fabricating services with the purchase of an aluminum awning manufacturer driven to the brink by air conditioning. This resulted in single source ordering for aluminum anodizing, aluminum extrusions & sheet, and fabricating – wins for both customers and SAF.
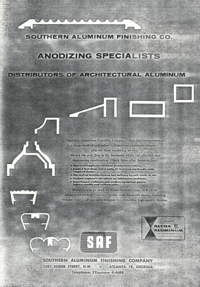 |
Magazine advertisement from the early 1950s. |
In 1968 after paint technology proved viable for architectural aluminum SAF began applying PVDF (aka Kynar® - a registered trademark of Arkema Inc ) paint coatings. Expanding its paint finishing services ten (10) years later in 1978, SAF commissioned a 20,000 sq ft, state of the art Fluoropolymer aluminum paint line. At this time SAF was among the first architectural fabricators in the US with an in-house aluminum paint line, offering customers another reliable aluminum finishing option with extensive color choices.
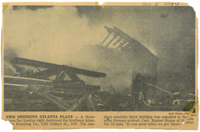 |
An old newspaper clipping serves as a somber reminder of a fire in 1954 that destroyed SAF's plant. Not to be done in by the tragedy, the company was back in operation in less than 8 weeks. |
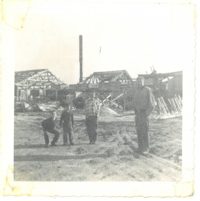 |
Founder Marvin McClatchey with three of his sons inspecting the progress of rebuilding the plant after the 1954 fire. |
In 1990 SAF entered the engineered architectural building products market by forming SAF Perimeter Systems Div. to manufacture innovative, custom commercial metal roof edge products, gutter & cornice systems. By 2011 the division had expanded its commercial Designer Series product offerings to include interchangeable extruded Cornice Mouldings, Gutters, Arch & Radius building trim systems in addition to entryway Pediment, Entablature and Column systems.
In 1994 SAF secured a resource for volume anodized aluminum sheet production by purchasing an aluminum Coil Processing plant. SAF’s coil-anodizing line gives their sheet customers substantial cost-savings. The plant also enables SAF to offer toll coating and related aluminum coil processing services. SAF is currently one of a handful continuous aluminum coil anodizers in North America.
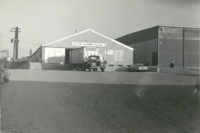 |
Above is the SAF plant as it looked in the 1960s. Below is a photo taken in 1987 in front of the building, with Marvin and sons, plus a couple of visiting businessmen from Japan. |
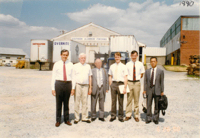 |
Growing sales led SAF to acquire a 78,000 sq ft metal fabrication facility in 2003, expanding capacity for both SAF Metal Fabrication and SAF Perimeter Systems Divisions. To speed customer service in 2004 SAF inaugurated unique programs of “1 Day out” and “3 Day Out” turnaround times for qualified aluminum finishing and popular fabrication services. An industry first, customers were quick to respond with orders. In pre-recession 2008 SAF reported sales of $32MM, and they reached $38MM in 2016.
 |
Despite being around for so long, SAF has kept pace with technological advances, offering top-quality products produced at state-of-the-art facilities. Shown above are anodizing tanks at the Redding, California operation. |
The pace of SAF innovation quickened with the introduction of architectural building column covers (2004) and panel (2007) systems, BIM CAD services (2009), Perimeter Systems engineered product innovations and enhancements. The company’s most remarkable physical expansion began after the opening of their SAF-West branch in Redding, CA in 2007. In 2013 SAF commissioned an anodizing line in Redding, transforming SAF-West to become a full mirror of SAF Georgia operations. This provides customers nation-wide with strategic benefits in price and delivery for all SAF services, including aluminum finishing, aluminum distribution, and fabrication projects. In 2015 SAF employment nation-wide reached 300.
About SAF
SAF (Southern Aluminum Finishing Co., Inc.) is a complete resource for metals distribution, finishing, and fabrication.
SAF is a mill-direct buyer of aluminum, aluminum coil and extrusions, as well as a fabricator of ACM systems. To learn more, visit www.saf.com.