Life Cycle Analysis And Aluminum Exterior Building Components
By Ben Mitchell, MBA, AkzoNobel and Vikas Ahuja, thinkstep
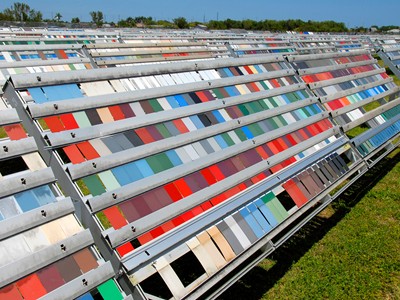 | |
Painted panels are tested for weathering at a facility in South Florida per AAMA standards. | |
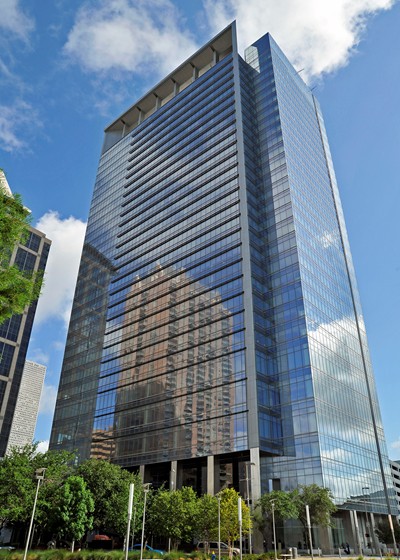 | |
Modern curtain walls feature engineered systems that successfully interrupt thermal bridging and prevent energy transfer. | |
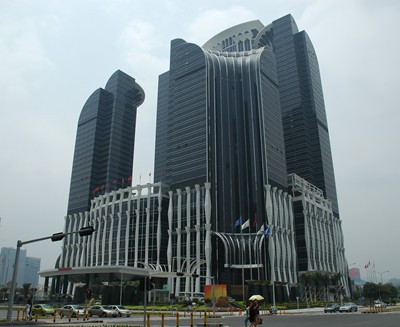 | |
High-rise wall surfaces are challenging to repair, so initial choice of finish is crucial. | |
Multiple environmental considerations must be taken into account when designing metal architectural systems, including curtain walls, panels, commercial windows, sunscreens and louvers. Fortunately, Life Cycle Analysis (LCA) and its associated tools are helping architecture/engineering/construction professionals address these considerations. LCA offers ISO guided, science-based, standardized measures of environmental performance. Assessment can be performed for a specific product, a system or a whole building and includes ALL stages of use, from raw material extraction through end of life (i.e., cradle-to-grave). Many third-party green building rating systems, such as the Architecture 2030 Challenge for Products and Leadership in Energy and Environmental Design (LEED), award points for buildings with Whole Building LCA and the use of products with EPDs.
LCA has grown out of the simple energy analyses that became common in the 1960s and now includes examining the overall environmental burden of products and buildings. Recent efforts have focused on standardizing the methods of communicating environmental impacts, as well as organizing and quantifying costs. As a result, product category rules (PCRs) and environmental product declarations (EPDs) have been developed as part of the LCA framework.
PCRs are defined in ISO 14025, Environmental Labels and Declarations – Type III Environmental Declarations, as “a set of specific rules, requirements and guidelines for developing Type III environmental declarations for one or more product categories.” Consensus-based documents developed by stakeholder organizations, they set parameters for the type of data used in an EPD. Per ISO 14025, there must always be a PCR before a manufacturer can produce an EPD. EPDs contain a summary of LCA results and are the documents used directly by a designer – however, it is necessary for designers to become familiar with PCRs as well as EPDs as a means of verifying that individual EPDs comply with methodological prerequisites.
LCA databases (e.g., Tally®, an Autodesk® Revit® plug-in) allow the designer to do Whole Building LCAs and benchmark environmental impacts throughout the design process. Databases are populated with industry-wide average life cycle impacts and product-specific EPDs, making design scenario comparisons fast, flexible, and easy.
Aluminum Building Components And LCA
Aluminum exterior building components contribute to the environmental performance of a building in various ways. Some of the benefits of aluminum are intrinsic. For example, 65% of all the aluminum ever produced is still in use and recycled aluminum uses only 5% of the energy required to produce primary aluminum. Furthermore, aluminum can be recycled over and over with no loss of physical properties. The aluminum recycling industry has tripled in recent decades, due to the material's increasing popularity.
Environmental impacts associated with the pretreatment and/or finishing phase of aluminum require particular consideration. Anodizing, for example, involves an electrochemical process that increases the thickness of the naturally occurring, protective oxide layer. This finishing option has some benefits: it is cost-effective; results in a very hard, mar- and scratch-resistant surface; and has a popular metallic look. However, it is also water-intensive, using millions of gallons a year. It requires the use of corrosive acids and chemicals, along with extremely high electricity consumption (which is typically generated using carbon fuels).
Buildings that use architectural coatings avoid the problems associated with anodizing. And while the chromates used in pretreatment methods have historically had environmental costs, those are being mitigated by the adoption of trivalent chromium or chromium-free pretreatment methods. To eliminate the use of chromium in the pretreatment process, conversion coatings have been developed that use "dry-in-place," nonreactive coatings that are applied in a thin film on the metal.
Benefits During The Use Phase And End Of Life
Other life-cycle benefits associated with the use of aluminum are conferred during building service life and stem from recent technological improvements to enclosure systems. The operational phase (i.e., the “use phase”) of a building causes by far the greatest environmental impacts. Historically, glazed openings were major points of unwanted heat loss or heat gain for building interiors. Exacerbating the problem was the fact that alloyed aluminum is highly conductive. But the advantages of glazed aluminum fenestration products ensured their continued popularity and drove several advancements in their technology.
In the last century, low-E coatings and insulating glass units (IGUs) improved the thermal performance of glazed openings immensely, since the glass itself represented the largest surface area over which thermal transfer occurred. Another significant thermal path, or bridge, was that of the spacer. Replacing the traditional aluminum spacer with warm edge spacers (constructed from low-conductivity materials such as polymers or low-conductivity stainless steel) was a first step toward improving framing. Although remaining thermal bridges in these systems were small, they were also significant, especially considering that more and more high rise structures were being designed to have curtain walls.
Curtain walls are comprised of a thin, typically aluminum-framed system with infill panels that are usually made of glass. Early curtain wall frames consisted of an uninterrupted metal cross section, which created a thermal bridge. But engineered systems—polymers or structural plastics set into specially-designed channels—successfully interrupt this bridge and prevent energy transfer.
For low-rise commercial or residential structures, metal roofing systems can lower air conditioning costs, reduce peak energy demand and help mitigate urban heat island effects. Metal roofing substrates are typically aluminum, galvanized metal or zinc/aluminum coated steel; coatings are applied to these metals in a factory setting. In addition to the environmental benefits conferred by the metal itself, some specialty coatings contain ceramic and inorganic infrared reflective pigments that are designed to reflect infrared energy while still absorbing visible light energy. Reflective pigments appear the same color as traditional pigments but stay much cooler, lowering attic temperatures by up to 35 degrees.
At the end of a building's service life, aluminum building components can be infinitely recycled, thereby avoiding the environmental burden of landfilling and offsetting the energy demands of aluminum production.
Product Service Life: Durability And Maintenance In The Use Phase
Another common measure of a product’s environmental impact is durability. The strength of aluminum framing members can meet standards for impact resistance (against wind-borne debris, etc.) as well as for blast loads (tested to 40,000 psi without steel reinforcement). Metal roofing is durable enough to be specified (along with other nonflammable materials) by some local codes, especially in areas prone to forest fires.
Any aesthetic or functional deterioration of a coated metal risks shortening the service life of a building or creating the need for extensive repairs. The extent of building surface area involved in high-rise architecture can make repair and refurbishment particularly challenging. Therefore, considerations such as the building finish become crucial.
Standards established by the national trade association American Architectural Manufacturers Association (AAMA) are voluntary and include specifications, performance requirements and testing procedures for pigmented organic coatings on aluminum extrusions and panels (for factory-applied organic coatings only).
As defined by the AAMA:
• AAMA 2603 identifies pigmented organic coatings that will provide a good level of performance, highlighted by one year of 45 degree South Florida weathering.
• AAMA 2604 focuses on high performance organic coatings that will provide and maintain a high level of performance that requires five years of South Florida weathering.
• AAMA 2605 focuses on organic coatings that will provide and maintain a superior level of performance that requires a 10 year South Florida exposure.
Coatings meeting the AAMA 2605 standard are appropriate for use on high-end building exteriors and are expected to last the lifetime of the building.
A related consideration when choosing a coating is the use of conflict minerals (those extracted in a geographic conflict zone and believed to fuel continued conflict). It is advisable to work with a coating supplier that can provide a policy statement on their product that is in accordance with the U.S. Securities and Exchange Commission (SEC) final rule on Conflict Minerals.
Designers and specifiers must develop an increasingly sophisticated understanding of how various products and materials will impact the environment. General terms such as "green" and "sustainable" are giving way to more specific and standardized measures of products' and buildings' environmental performance. Therefore, understanding PCRs, EPDs and LCA, as well as the software tools that assist in their implementation, is now critical for any designer.
About The Authors
Ben Mitchell, MBA, is the extrusion coatings sales and marketing manager for AkzoNobel, a global paints and coatings company and producer of specialty chemicals. He has a bachelor’s degree in comprehensive science as well as an MBA from Urbana University in Ohio. Mitchell started at AkzoNobel in 1990 as a lab chemist formulating PVDF coatings, and moved into product management. He can be reached at ben.mitchell@akzonobel.com.
Vik Ahuja is a Sr. Account Executive with thinkstep, a global leader in LCA consulting, sustainability software development, and lifecycle inventory databases. Ahuja has a BS from the University of Chicago and an MBA from the University of South Florida. He has niche expertise in LCA, sustainable construction, and environmental transparency programs. He is based in Chicago and can be reached at vik.ahuja@thinkstep.com.
About AkzoNobel
AkzoNobel manufactures coil and extrusion coatings for metal construction. For more information, visit https://coilcoatings.akzonobel.com/us.