Sturdy And Stylish: Coil-Anodized Aluminum Provides A Host Of Benefits And Helps Bring Modern Designs To Life
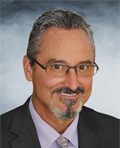 |
Phil Pearce |
By Phil Pearce, Vice President of Global Sales and Marketing for Lorin Industries, Inc.
While metal products have proven to offer many benefits when compared to competing cladding materials, few are as uniquely suited to exterior architectural applications as coil-anodized aluminum. Its unmatched durability, extreme light weight, high strength-to-weight ratio, and easy installation make it a highly functional material, while its three-dimensional look and ability to be colored to match project needs ensure superior aesthetics. Anodized aluminum can provide an appearance similar to a number of different metals for architectural applications, but oftentimes with lower costs and better weathering resistance. This article will help explain the benefits of anodized aluminum and provide inspiration for how to best leverage its unique characteristics when creating great building projects.
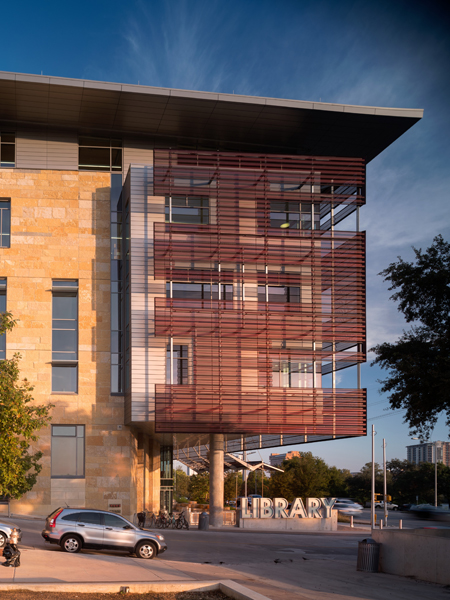 |
Perforated anodized aluminum is a central façade design element in the recently constructed central library in Austin, Texas. Photo credit: Nic Lehoux |
Stylish aesthetics complement versatile function
The coil anodizing process, pioneered by Lorin Industries, Inc. in 1953 provides the aluminum with a protective layer that improves its aesthetic properties and durability. Continuous coil anodizing forms a clear, translucent oxide layer that protects the metal, shows the metal’s natural beauty, and is consistent over every inch of aluminum. The three-dimensional crystalline structure of the aluminum oxide layer also reflects and refracts light in ways that help the surface come alive. Unlike paints or coatings, this oxide layer is grown from the raw aluminum and bonded at the molecular level so it cannot chip, flake or peel like paints and coatings.
When metal fines are added to the coil anodizing process, anodized aluminum can be made to mimic almost any other metal, including brass, copper, zinc, bronze, gold, silver, stainless steel, titanium, or carbon steel. Anodized aluminum, however, does not tarnish like brass, patina like copper, or fade like bronze, so these metal looks are UV stable.
Anodized aluminum is as much as 2/3 lighter than other metals. It thus offers a significant cost advantage, as the aluminum itself is often less expensive per square foot than other metals, and far fewer pounds of material are needed for any given application. This not only helps with costs for the anodized aluminum products, but it also contributes to the cost savings for structural aspects of the project, as the structure does not need to support significant added weight as in the case of copper or steel.
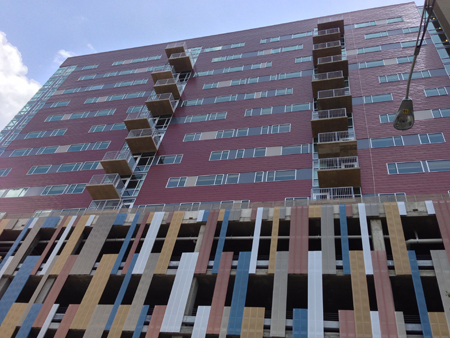 |
A student housing building at the University of Texas at Austin (2400 Nueces). Lorin anodized aluminum is used to make shingles that are incorporated into the façade design, and perforated anodized aluminum sheets on the building’s garage help the building to meet ventilation requirements while coordinating with the overall building design. Photo Credit: Lorin Industries, Inc. |
Functional benefits for architectural exteriors
The molecular structure of the aluminum oxide layer formed by the coil anodizing process is hard like sapphire, which is second in hardness only to diamonds. This oxide layer thus provides long-term durability, as well as corrosion and abrasion resistance. It is also self-healing if damaged as the aluminum will naturally create its own protective oxide layer where it is exposed to the elements.
Anodized aluminum also offers additional benefits for long-term maintenance beyond its unmatched durability. Unlike some paint warranties that require cleaning every year, Lorin’s anodized aluminum only needs to be cleaned every other year if it is on the exterior of a building, thus providing some really significant maintenance cost savings.
Although natural metals are a commodity and therefore prices can have a degree of volatility, generally due to its high strength to weight ratio, anodized aluminum can cost as much as 60-70% less per square foot than many other natural metals.
Coil anodizing delivers consistent quality, and the handling and installation is simple as the material is light and workable. This solves many challenges faced in construction due to rigid or heavy materials. Many anodized aluminum panels can be installed on buildings with standard hand tools, not requiring the expense of a crane as is the case with inherently heavier materials.
Coil-anodized aluminum can also be perforated in a variety of patterns to a range of percentage openness before anodizing. Perforated aluminum serves both functional and decorative purposes. When used on building or garage exteriors, it can provide noise control, improved HVAC efficiency, screening of sunlight and/or environmental particulates, and management of a structure’s wind or heat loads. At the same time, it enhances the aesthetics of the building façade. Engineered correctly, perforated aluminum will last throughout a building’s lifetime.
Applications for anodized aluminum
Anodized aluminum can be used for a wide range of architectural and construction applications, including building facades, curtain walls, roofs, column wraps, and lighting. Building facades can be installed as honeycomb panels, ACPs (Aluminum Composite Panels), solid metal panels, and roll formed panels. Other common uses include trim, signage, and sunscreens.
Lorin’s anodized aluminum products are available with Architectural Class I and II films and are offered in colors that are UV stable and can be used in coastal areas. With functional benefits of a high strength-to-weight ratio and superior durability, and the aesthetic benefits of a beautiful natural metal look in a variety of colors, anodized aluminum is uniquely suited to bring innovative architecture designs to life for building exteriors.
About Phil Pearce
With over 37 years of sales and marketing experience, 27 of which he spent focused on the architectural industry, Phil Pearce is the Vice President of Global Sales and Marketing for Lorin Industries, Inc. In this role, Pearce oversees strategic domestic and international sales and marketing for Lorin.
Pearce brings decades of expertise to his work in customer relationship management, market development, project solutions, and product development. Additionally, Pearce oversees the work of a number of teams within Lorin Industries, including sales, distribution, marketing, and customer care. Pearce’s architectural industry and sales expertise contribute greatly to Lorin’s success and customers’ satisfaction.
About Lorin Industries
Lorin
Industries is a provider of coil anodized aluminum, used in various industries including architecture and construction.