Proper Design And Detailing Remain Critical As Metal Roofing Sales Continue To Grow
By Travis Lord, The Garland Company Inc.
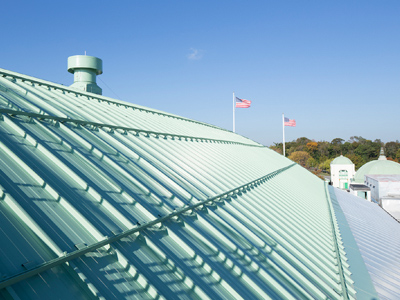 |
RMer Span roofing by Garland. Photo credit: Christian Scully/Design Imaging Studios |
For years, the stigma surrounding the upfront costs and complex installation of metal roof systems has kept some building owners and architects from exploring further. They would go with a system they knew or one they had always used, likely replacing
it at least once (if not more) in the time one metal roof system is designed to last. But things are starting to shift. Metal roofing sales are expected to grow significantly in the coming years with revenue in both the commercial and residential
markets projected to reach a combined $4 billion by 20201. The growth will be driven by improved contractor training, increased acceptance among building owners who more fully understand the long-term performance benefits of metal roofing,
and new construction starts.
Additional key factors supporting the strong growth expected in the market, as cited by Principia Consulting, a leading research and consulting firm focused exclusively on the building materials and construction industry, are as follows:
“Greening” Of North American Construction
Metal roofing will continue to be a popular choice as energy savings and other environmentally friendly aspects of the material assert a stronger appeal to building owners.1 A properly designed standing seam roof system can provide energy savings
of up to 40 percent. In fact, an Oak Ridge National Laboratory study found that metal roof systems are more effective than conventional roofs in reflecting the sun’s rays and in preventing solar heat transfer into the building, which can reduce
air conditioning costs.2
Life-Cycle Cost Awareness
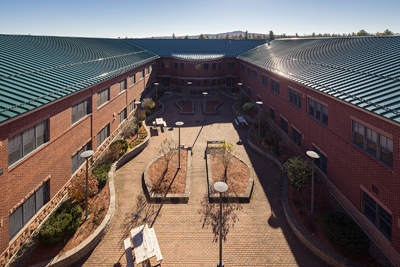 |
RMer Shield roofing by Garland. Photo credit: Christian Scully/Design Imaging Studios |
More building owners are beginning to understand and appreciate the importance of using a life-cycle cost analysis to evaluate the total cost of roof systems versus just the initial cost. A Ducker Research Company study found metal roofs have an expected
service life of 40 years or more, putting per square foot costs around $0.30 compared to $0.57 per square foot for single-ply. The percentage of total installed costs spent on maintenance was also drastically lower for metal roofs than it was for
asphalt or single-ply.2
More On-Site Roll Forming
On site roll forming is expected to continue to expedite the supply chain. The use of on site roll forming can reduce freight costs on certain projects. In addition, using a roll forming machine allows for continuous panels, which helps to increase the
strength of the waterproofing system and lessen the amount of maintenance required to provide an overall lower cost of ownership.
Details Matter
So as this sector of the industry continues to grow, it’s important to understand that the successful performance of any roof system, but especially metal roof systems, is highly reliant on proper design and detailing. As the saying goes, “the
devil is in the details”. Details can truly make or break a standing seam metal roof system, which is why proper design and waterproofing techniques are critical to achieving the system’s intended performance life. Oftentimes, due to various
factors like the complexity of the roof system, inexperience with the materials being installed, or expedited schedules, details can be missed or installed improperly. Although it may seem harmless at first, those small problems will likely become
bigger, more costly issues down the road, which is why it’s important to get it right the first time. And it helps to know where the most common problems occur so those areas can be designed with extra precision.
Seam Conditions
The design of the seam is probably the most important element to a standing seam metal roof and choosing the most effective design helps set the foundation for the performance of the roof. The majority of standing seam systems use a one- or two-piece
clip. Two-piece clip designs use a base that fastens to the substrate, which is attached to the second sliding piece. These are meant to withstand the thermal expansion and contraction of the metal roofs, but only at a limited capacity. For example,
70-foot metal panels can thermally expand and contract up to two inches; some two-piece clips cannot handle that much movement. Along with that, these clips have to be installed in the perfect location to account for ambient and panel surface temperatures
and anticipated changes – a step often overlooked during installation. As a result, panels can bind on the clip, which, in turn, can cause the dreaded oil-canning effect.
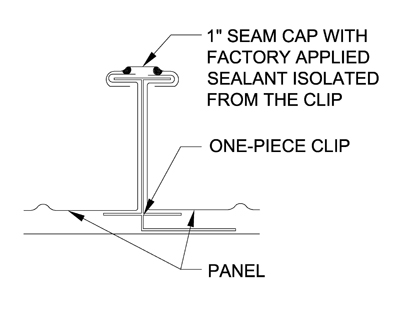 |
One-piece clip and factory-applied sealant that is isolated from the clip. Photo credit: The Garland Company |
Consider using a one-piece clip to avoid those potential issues. A properly designed, structural one-piece clip can allow for unlimited movement as long as the roof panels were designed to accommodate the anticipated movement. The panels simply sit or
float on the clip, which is typically fixed at the ridge, allowing the entire roof system to move from the fixed point without issue. The one-piece clip design also removes the potential for installation error, as there is no “perfect”
position necessary to set the clip.
Along with the clips, the sealant in the seam is a critically important part of this detail to understand. Sealant in direct contact with the clip will eventually be worn away due to thermal movement of the panel. Without proper sealant, the seam is no
longer waterproof. The potential for problems, such as inconsistent application rates, increases even more if the sealant requires field application. Significant labor costs can also be added to the project in this case.
A better alternative is a seam design where the sealant is factory applied and isolated from the clip. To properly separate the clip and sealant, the panel legs that create the seam need to be shaped in such a manner that they surround the clip. Then,
a separate seam cap with the factory-applied sealant can be installed over the top. Since the panel legs wrap around the clip, the sealant is isolated, allowing the seam cap and panels to move over the clip without any sealant deterioration. The factory
application eliminates the need for an installer to field-apply the sealant, removing the risk of mistake or incorrect application rates.
Ridge Conditions
Many ridge conditions on standing seam roof systems are installed with too few layers of waterproofing or with conditions that aren’t built to last. The two most common are foam closures installed with a bead of sealant and end panels cut and folded
upwards.
Here is what typically goes wrong.
Foam closure: It is adhered with a sealant that is not held in compression against the panel so the sealant may not bite and completely hold the foam in place. Over time, the sealant will deteriorate, causing the foam closures to become loose and
eventually fall out.
Cut and bent panels: Wind driven water can find its way through those cut sides and into the building.
Here are better options.
 |
Head closure with the sealant being installed. Photo credit: The Garland Company |
Metal closure: Instead of using a piece of foam in an adhesive, put the foam into a metal closure piece that is fastened in place under the ridge cap. The foam is kept in compression and the metal houses and protects it from falling out. A bead
of sealant should be placed on the backside as well as the front side of the closure to act as secondary waterproofing.
Bent panel: The panel can be bent upwards as in the example above. However, a proper tool should be offered by the manufacturer that will eliminate the need for the panel to be cut and remove any potential entry point for water.
Valley Conditions
Valley details on standing seam metal roof systems are commonly under detailed with only a single layer of waterproofing used – typically a piece of valley foam with butyl sealant. Since the valley is strictly used to direct water off the roof,
it will be highly susceptible to infiltration if not detailed correctly. A more effective method would be to use multiple components to keep the water out so if one method fails, there’s another already in place. It is important that the panels
have the ability to expand and contract at the valley; the fixed point should be at the ridge/head condition. The metal valley closure should be riveted to the end of the panels to serve as the first layer of waterproofing for this part of the roof.
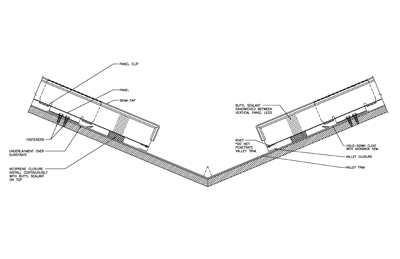 |
Valley condition showing all of the waterproofing components. Click to enlarge. Photo credit: The Garland Company |
Next, a valley closure foam should be self-adhered to the valley pan behind the metal valley closure. Two beads of non-curing butyl sealant should be applied to the top side of the valley closure foam and then run up the panel legs into the seam. For
roofs with low slopes, especially in regions with heavy snow, two rows of closure foam should be used. The third and final mode of keeping water out of this detail includes a kickback, or hem in the valley trim, similar to the pan-end bending of the
roof panels in the ridge detail. This will be behind the valley closure and the foam. Together, these three waterproofing components work to make the valley impenetrable to moisture. A high temperature rated metal roofing ice and water shield underlayment
should also be used whenever possible for additional protection.
Eave Conditions
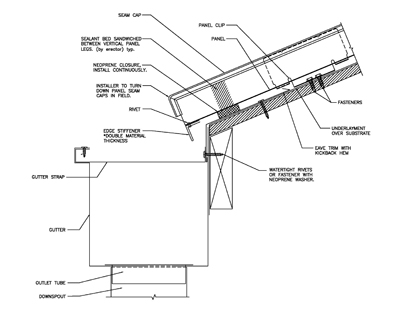 |
An eave detail showing all of the components. Click to enlarge. Photo credit: The Garland Company |
The eave detail is extremely critical to get right, as it is one of the most vulnerable areas on the roof. The profile designs of many panels make this area exceptionally difficult to keep watertight. For example, a trapezoidal style panel has a large
void at the end of the seam that needs sealed. In most cases, a foam closure, similar to the head/ridge detail, is installed with a sealant. Once the sealant starts to deteriorate, the closures can become loose and potentially slide out from under
the panel, making the system susceptible to water intrusion. On top of that, most systems will have a gutter as well. If the gutter is improperly made or is an internal gutter, water can flood into the building in the event the gutter backs up. The
same “belt and suspenders” approach to waterproofing used when detailing valleys should be used here as well. The first layer of protection is an edge stiffener, which acts just like the valley closure. The second layer should include
self-adhered foam with two rows of non-curing butyl sealant on top and up the seam legs. Lastly, behind the first two waterproofing layers, the eave trim will have the kickback hem. Regular maintenance of the gutter to ensure it is free of debris
such as dirt and leaves is also critical to allow water to flow freely out of the gutter.
Summary
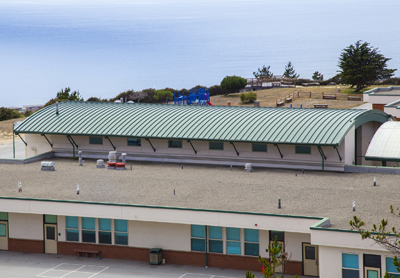 |
RMer Span roofing by Garland. Photo credit: Christian Scully/Design Imaging Studios |
Most metal roof systems are designed to provide the longest watertight protection of any other type of roofing material. But that’s only the case if the system is properly designed, detailed and installed. To do that, work with a trusted team of
experts, including a designer, building owner, contractor and manufacturer’s representative who is actively involved with the project from start to finish and is dedicated to a preventative maintenance plan. Along with that, rely on the proven
“belt and suspenders” waterproofing methodology to ensure the system lasts its intended lifetime (or even longer).
Travis Lord has more than five years experience developing industry-leading metal roofing, wall and edge systems for the commercial building envelope. As a product manager at Garland, Lord is also responsible for training Garland’s field team in the proper installation and detailing of those metal systems. Lord graduated from The University of Central Florida with a bachelor’s degree in mechanical engineering. Garland is a Cleveland-based manufacturer of high-performance solutions for the total building envelope.
References
1. Olson, Casey, Metal Roofing Market Strong and Building Momentum, Principia Consulting, 2018, Retrieved from: https://www.principiaconsulting.com/metal-roofing-market-strong-and-building-momentum/
2. Russ, Rodger, 6 Reasons to Consider a Metal Roof, Buildings, 2013, Retrieved from: https://www.buildings.com/news/industry-news/articleid/16143/title/6-reasons-to-consider-a-metal-roof/viewall/true
About Garland
The Garland Company Inc.'s product line includes metal roof and wall systems, metal soffits and metal roof recoating products. For more information,
visit www.garlandco.com.