Bradbury Provides Roll Forming Solution For Leading HVAC Accessories Manufacturer
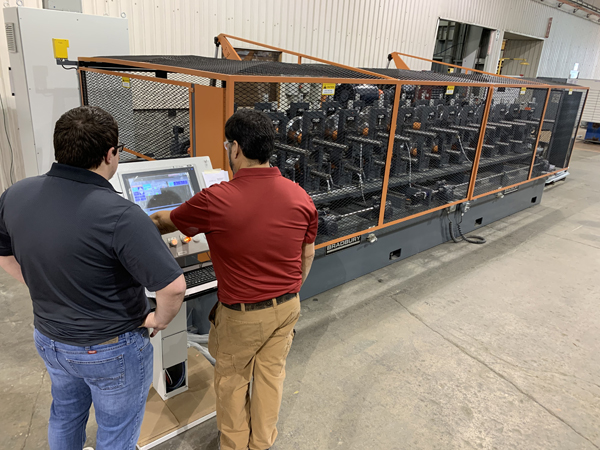
Moundridge, KS - MicroMetl is the nation’s largest independent manufacturer of accessories for commercial heating and cooling equipment. Recent changes in its product mix put MicroMetl in a position where major advancements had to be considered
for its production process if the company wanted to remain competitive. For help with that process, the company turned to The Bradbury Group.
“We’re always looking at ways to do a better job for our customers,” says Brandon Schultz, CIO of MicroMetl, headquartered in Indianapolis. “To be competitive we must produce high-quality products in a cost-effective manner, so
we have to continually look for ways to drive down the cost of production. We have been doing this for 56 years, and we need the best tools to stay competitive. So, with the change in our product mix, we went to our engineers and asked them, how can
we be faster and cheaper?”
Ultimately, the change in product mix required MicroMetl to be more flexible when it comes to production.
“We wanted to increase our manufacturing flexibility and capacity to meet our customer demands in a more efficient manner,” says Scott Nelson, MicroMetl’s Senior Manufacturing Engineer. “Our existing roll former was aged and would
not adjust for the flexibility we needed.”
MicroMetl originally reached out to Bradbury in 2017 and again in 2018, trying to make an educated decision on what was needed to make the MicroMetl operation more efficient.
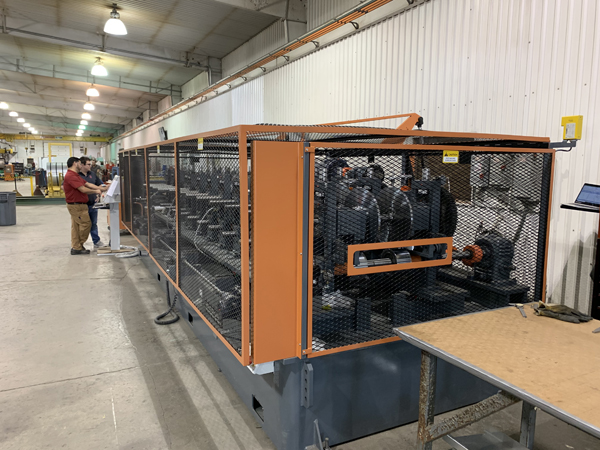
“Fast forward to March 2020, we were approved to purchase a new roll former, but on a tight timeline,” Nelson says. “Bradbury had a rep at our facility in Indianapolis almost immediately and right at the beginning of the pandemic. Within
three weeks, we had the quote from Bradbury on the custom design and a purchase order was sent confirming the sale. I feel all our requests and requirements were met in a timely fashion to help bring this project to fruition, especially challenging
during a year of uncertain times.”
MicroMetl’s main contacts at Bradbury were sales representative Zack Ledford and project engineer manager Scott Miller.
MicroMetl purchased a 420-3-12P-STR (Single Telescoping Roll Former) to manufacturer HVAC panels for knockdown rooftop curb adapters.
“Zack and Scott were in constant communication with me during the design phase, which was crucial to getting the project off on the right foot, Nelson says. “They were readily available for any questions throughout the process and communicated
with us in a timely fashion.”
Nelson worked directly with Bradbury engineers to investigate the possibility of a roll former that could do everything MicroMetl needed. “We visited Bradbury (in Moundridge, Kan.) and they basically took us through a Roll Forming 101 class,”
Nelson says. “We spent four days at Bradbury, learning about our machine and roll forming in general. We tested our parts and worked through any programming issues. When it was time to sign off, we had our closing meeting with all the individuals
who helped make the project a success during the design and going forward during installation and maintenance.
“Our old roll former could produce a one-size part. Any changes to that part had to be made on the press brake, by a highly skilled and highly paid operator. With our new roll former, with the push of a button, we can go from producing our smallest
part to our largest part in less than two minutes. The roll former is the solution to performing 90 percent of the work we need without using the press brake or outsourcing any work.”
MicroMetl can now manufacture panels with varying size webs, legs and lips. The old roll former manufactured one size web, leg and lip. “We can reduce our changeover time dramatically with the automated system that quickly changes from one curb
size to another in a matter of minutes,” Nelson says. “We can feed multiple gauge thicknesses through the roll former without adjusting by using the BardieTM Cartridge Technology. That’s extremely helpful in our deck pan
manufacturing where different gauges may be in the same stack of blanks.”
MicroMetl has reduced the number of hours needed on press brakes to manufacture curbs that could not be made on the old roll former. That frees up press brakes (and operators) to form other parts that are currently being outsourced. “We have reduced
the number of hours to complete a job compared to press brakes,” Nelson says. “We have also reduced overall scrap of knock-down curb adapters because the precision of the roll former compared to the press brakes.”
“The overall experience was a lot easier than I thought it would be, because of the expertise at Bradbury,” Nelson says.
About The Bradbury Group
The
companies of the Bradbury Group are known for the cutting-edge
technology and reliability built into every product – and for the
exceptional service that helps satisfy customers worldwide. Bradbury
strives to set the standard for automated production and systems
integration in the metal processing industry. Bradbury believes its
leveling, cutoff, punch, folding, roll forming machines and automated
systems set the highest standard for productivity, reliability and
safety in coil processing. To learn more,
visit www.bradburygroup.com.