Continuous Coil Anodized Aluminum Offers Benefits For Exterior Façades
By Phil Pearce, V.P. Global Sales & Marketing, Lorin Industries
Continuous coil anodized aluminum offers significant benefits for exterior façades. An excellent alternative to applied coatings like paint, continuous coil anodized aluminum provides a durable, consistent, and elegant appearance combined with
lower maintenance costs and significant environmental benefits.
Continuous Coil Anodized Aluminum Basics
Continuous coil anodized aluminum uses a tightly controlled electrochemical process to grow an aluminum oxide layer from the base aluminum by converting the aluminum into aluminum oxide, so it is bonded at the molecular level unlike an applied coating.
Raw aluminum, while more naturally corrosion resistant than other metals, will produce its own oxide layer, but this layer is soft, opaque, and very thin compared to pre-anodized aluminum where the anodic layer is much harder, thicker, and translucent.
Coiled raw aluminum is unwound and cleaned, then pulled through a series of tanks that clean, anodize, color, seal, then rewind the coil all in one continuous process. Coils are placed at the start of the process and remain unhandled until the end of
the process, resulting in less scrap and lower costs. Figure 1 is a graphic overview of the process.
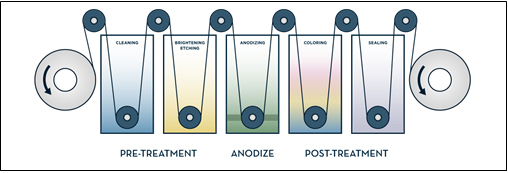 |
Figure 1. Continuous coil anodized aluminum process. Courtesy Lorin Industries |
This uniform anodic layer results in a very consistent surface appearance with elegant colors, and unlike applied coatings like paints, it can never chip, flake, or peel. In addition, the anodic layer is actually a crystalline structure, so it can reflect
and refract light in ways that help the material come alive and change with changing light conditions. The end result is an enhanced aluminum surface that provides cost and production efficiencies, beauty, versatility, and sustainability.
Exterior applications include building façades, curtain walls, roofs, column wraps, and lighting. Building façades can be installed as honeycomb panels, aluminum composite panels, solid metal panels, and roll formed panels. Other common
uses include trim, soffits, gutters, signage, backsplashes, and ceiling panels.
These anodized finishes are a great choice for a wide range of structures, from mid-range storefronts, institutional buildings, schools and government buildings to monumental commercial industrial buildings, residential, high traffic areas, storefronts,
handrails, entry systems and windows. Pictured at the end of this article is a gallery of a few high profile buildings around the world featuring continuous coil anodized aluminum provided by Lorin.
Advantages Of Coil Anodized Aluminum For Building Exteriors
Appearance – Coil anodized aluminum offers the structure and appearance of a sapphire. The clear, translucent oxide layer does not cover up the natural beauty of the metal below; rather it helps the metal’s natural beauty shine through.
The authentic natural metal look accentuates the aluminum’s rich metallic appearance.
Anodized aluminum is extremely color consistent and will not chip, flake, or peel, nor does it chalk, blister, or creep. When UV stable colors are used, the anodic layer is guaranteed to retain its color, reflectivity, and gloss for a minimum of 10 years;
some colors are guaranteed for 20 to 30 years, while others feature a warranty of 40 years. By contrast, paint coatings with 70 percent polyvinylidene fluoride or polyvinylidene difluoride (PVDF) resins may feature gloss and color retention warranties
ranging from 25 to 30 years, while those coatings with 50 percent PVDF resin may only have a 5 to 10 gloss and color retention warranty.
Health and environmental – The anodized aluminum material also has several health and environmental benefits. Unlike painted coatings, coiled anodized aluminum does not emit volatile organic compounds (VOCs), which are known for negative
health consequences and for contributing to climate change due to off-gassing when activated under sunlight.
In addition, clear anodized aluminum has better Solar Reflectance Index (SRI) values than paint, reflecting more heat off a building to reduce the urban heat island effect that can contribute to climate change. This can also mean reduced up front cost
for HVAC systems, and lower energy use over time, thus improving the return on investment (ROI) for lowering energy costs. Reducing energy consumption can also reduce pollution and warming effects resulting from energy production. The anodic layer
is also going to be cooler to the touch than oil-based paint products that retain heat.
Other environmental impact reduction stems from process improvements. For example, Lorin has reduced the environmental impacts of its electrochemical process by investing in cleaner burning natural gas powered engines to replace energy from coal-fired
power plants. Chemicals used in the process are reclaimed and recycled for reuse, and the process has been configured to eliminate the introduction of any waste into industrial wastewater flowing to the local municipal wastewater treatment plant.
All VOCs have been eliminated from the production process.
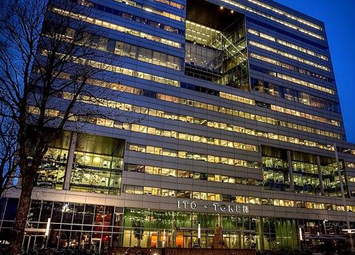 |
Ito Tower, Amsterdam |
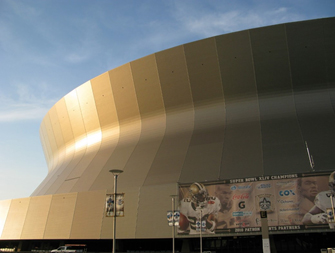 |
Louisiana Caesar's Superdome, New Orleans |
Hardness and durability – Anodized aluminum surfaces score a 9H on the pencil hardness (Wolff-Wilborn) test, similar to that of a sapphire, while that of PVDF paint is HB, in the middle of the scale. The anodized material also offers excellent
abrasion resistance and performs better than paint on the Tabor abrasion and falling sand abrasion tests. This means the anodized finish is more durable and keeps its original beauty even after being cleaned multiple times.
Corrosion and salt spray resistance – Coil anodized aluminum offers superior corrosion and salt spray resistance. Because salt water and air will not affect the anodized surface, the material is better than applied coatings for use in coastal
areas. In addition, some paint warranties are reduced if the structure is closer to the coast. By contrast, Lorin does not reduce its warranty because the salt air and water environment does not harm the anodized layer.
Reduced maintenance costs – Continuous coil anodized aluminum also reduces building maintenance costs, which means that it offers a better long term ROI than paint. The surface of the anodized aluminum is very smooth and dense, as well as
dielectric so it does not have static electricity, meaning it is not as easy for dust to collect on surfaces as it does on a painted surface. Also, being a hydrophobic surface, anodized aluminum resists water and dirt build up more than paint. No
special chemicals are needed for cleaning, nor does cleaning need to be performed as often. Many paint warranties require that the surface must be washed every year. By contrast, Lorin’s coil anodized aluminum warranty requires cleaning only
every other year, resulting in considerable savings over the life of the material.
Color And Price Comparison
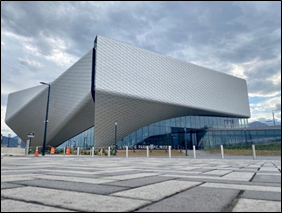 |
US Olympic Paralympic Museum, Colorado Springs |
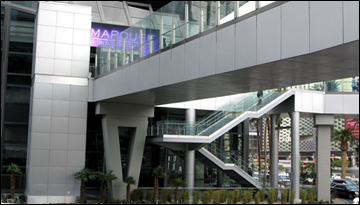 |
Las Vegas City Center, Nevada |
Coil anodized aluminum can be made in numerous colors. For example, Lorin can match most any natural metal look, including shades of zinc, steel, titanium, copper, gold, brass, bronze, and natural aluminum. For exterior use, anodized aluminum can be made
to simulate other metals using inorganic dyes or metal fines added into the pores of the protective anodic outer layer. Lorin has even matched Coca-Cola Red and Victoria’s Secret Pink. However, coil anodized aluminum is not available in UV stable
bright primary colors.
Clear anodized aluminum is comparable in cost to PVDF paints. UV stable colors cost in the range of up to $1 more per square foot.
Gallery Of Architectural Sites Featuring Anodized Aluminum
Continuous coil anodized aluminum has been used all around the world. A few examples of exterior façades provided by Lorin are shown.
First is the Ito tower in Amsterdam, winner of the prestigious Pritzker Architecture Prize and featuring Lorin coil anodized aluminum done with Hunter Douglas panels. Others pictured include Louisiana Caesar’s Superdome, New Orleans; the US Olympic
Paralympic Museum, Colorado Springs; and Las Vegas City Center, Nevada.
Additional examples include the Youth Olympics Games towers, Nanjing, China and the Gyeongju World Expo Tower, South Korea.
With its exceptional beauty, durability, and consistency of color, continuous coil anodizing has numerous advantages over painted surfaces for many building types and applications.
About Lorin Industries
Lorin
Industries is a provider of coil anodized aluminum, used in various industries including architecture and construction.