Retrofit Roof Design And Testing From The Early Days To Today
By Dale Nelson, President
Roof Hugger, LLC
32 years ago, in 1991, my partner Red McConnohie had an idea to create a retrofit system that would allow you to put a new metal roof over an old worn-out metal roof. Red and I formed our then-fledgling company, Roof Hugger, and set out to market our “new and better” product to metal building contractors and erectors.
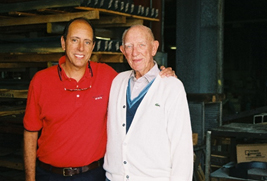 |
A vintage photo of Roof Hugger founders Dale Nelson (left) and the late Red McConnohie. |
Soon enough we started getting questions like “How do we know this is a structurally correct assembly?” Good question I thought, how do we confirm our retrofit system is as strong as we “knew” that it was. We had a design engineer
but in the early 1990s there was no standard test for what we were doing; we had pages of calculations but no actual tests. So, we called our engineer for some ideas on how to conduct testing.
Let’s build a roof section, he said, turn it upside down and stack concrete blocks on it until it collapses. We weigh the blocks, and then we’ll know at what load the system fails. Great idea we thought so off we went to create a mockup and
test it. The system didn’t perform quite like it calculated but we had some actual data points!
By the late '90s test labs were getting more sophisticated. The Celotex Test Lab Facility in St. Petersburg, FL recommended a then-precise protocol for uplift performance and we did some additional confirming tests, using the latest equipment. Now we
had even more data points to compare to our early rudimentary testing.
In the early 2000s a new test was becoming the industry standard for testing and for code compliance. This new test was the ASTM E-1592. Although testing for through-fastened panels was not considered necessary and calculated values were still being used,
there was no precise way to determine the capacity for the newer standing seam panels. The E-1592 test was developed to test standing seam panels, although it can test both types. It basically places a flexible airbag beneath the panel and air pressure
is gradually added to this airbag pushing the panel up until it fails. Very aggressive, but a reliable and repeatable test which soon became the industry standard.
This was the best test ever for our system because now we could have real performance test data with the sub-framing system and the actual new roof panel (or similar) in a real-world assembly. The testing confirmed what we had discovered from our earlier
tests, that the systems do not test as well as they calculate. However, this was good news, since now we had industry-accepted performance data! The only problem was that there are hundreds of new and existing panels in the market. Fortunately, many
panels are very similar and can be grouped for analysis, but a significant amount of testing still had to be conducted. With this knowledge, we set about the business of testing the major groups including Screw-Down Roofs, Vertical Rib Standing Seam,
Trapezoidal Standing Seam, Deep Rib Systems, Tall Clip Assemblies, Corrugated panels, and more.
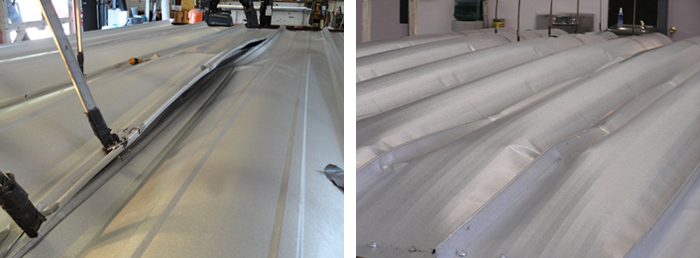 |
Today’s challenges are even more complex. We always knew that the notched retrofit framing systems added additional weight to the building; we also knew they added additional strength to the existing purlins, but to what extent? The existing building
code allows an additional 3 lbs. per sq. ft. of additional loading without a full building analysis, which will cover most building retrofits, however, we also knew this added strength research would be important because in some cases the existing
buildings were already loaded to their maximum. This was an interesting and challenging question since no real test protocol existed to make that determination.
In 2018 we began the first-ever Base Testing for a retrofit system on continuous purlins. This required the construction of a 50' long chamber and many combinations of parts and pieces. The results are in and very positive. Modeling of the results has
been completed allowing the analysis of most existing metal buildings, their current capacities, and the capacity after retrofitting.
This is great news for the designer/specifier. Retrofit metal roofing has come light-years from its humble beginnings. Shirt sleeve engineering has progressed to full system performance engineering with predictable results. Makeshift assemblies are recognizable
for their shortcomings and lack of confirming test data.
Roof Hugger’s acquisition by the LSI Group in 2016 has allowed us to do a greater and wider range of testing. Our history and ongoing commitment to fully understanding metal-over-metal retrofit has given us a depth of knowledge that surpasses anyone
producing metal-over-metal retrofit framing systems. A partial list of this testing includes:
• E-1592: Multiple profile combinations - PBR over PBR, standing seam over PBR, standing seam over standing seam (various profiles), PBR over corrugated, standing seam over corrugated, 7.2 rib over PBR, and more.
• UL-580/1897: Standing seam over standing seam attached to structural decking, testing over 2x10 wood purlins.
• FM-4471: Standing seam over PBR, standing seam over standing seam
• Diaphragm enhancement testing
• Drag-load testing
• Base Testing: Simple and continuous spans
• Computer modeling of purlin strengthening w/engineering confirmation from test results
• Hot Box Testing
• Testing of Roof Huggers with vent hole punching in vertical web
Testing is a slow and expensive process but it has come a long way from the early days of stacking of building materials on a test mockup. Our large volume of test data base has given us the understanding that not every retrofit system will perform exactly
like the panel tests alone might indicate. As a result, unless we have tested a particular assembly of new and old panels, Roof Hugger will typically reduce the panel test data by some percentage to provide a conservative and defendable design. Overkill,
maybe, but we have had no failures in our entire history and many stories of buildings surviving events way in excess of their design.
The fact is that all roofs will wear out at some point, even metal roofs. When that time arrives, it is good to know that by using Roof Hugger, you can specify, with confidence, a new long-life metal roof system, that will upgrade the existing buildings’
old roof to today’s stringent building codes or beyond.
About Roof Hugger
Roof Hugger notched sub-purlins enable replacement of new metal roof panels over an old metal roof. They can be used over
screw-down or standing seam roof systems and can accommodate new standing seam or screw-down panels. Roof Huggers also maintain integrity of original design loadings; achieve "thermal break" air space between old and new roof sheets; allow for
optional insulation; and are laboratory and load tested—with certified load charts. For more information on metal-over-metal retrofit re-roofing, contact Roof Hugger at 800-771-1711 or visit www.roofhugger.com.
