Installing And Disconnecting Lightning Protection Is A Job Better Left To Specialists
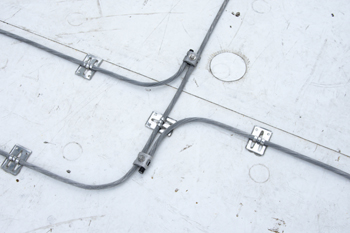 | |
Lightning protection standards contain specific requirements for conductor coursings, fastener placement and interconnection methods for joining conductors and building systems. | |
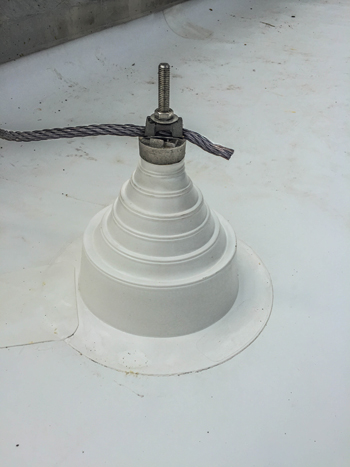 | |
This is a properly installed lightning protection system through-roof penetration. | |
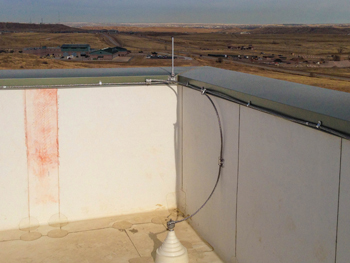 | |
Rooftop lightning protection components correctly installed along the inside of the parapet. | |
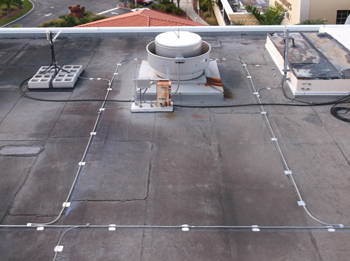 | |
A neatly installed, standard compliant, lightning protection system roof network. | |
 | |
An installer correctly connects and fastens a lighting protection system in this through-roof application. | |
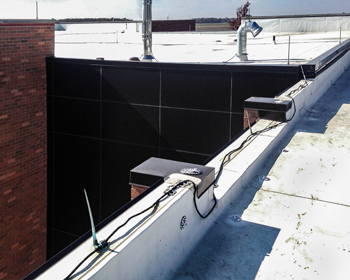 | |
Re-installing a lightning protection system requires special attention and the knowledge of a certified installer. After completing some roofing work on this project, this system is reinstalled correctly: the conductors are straight, no
sharp bends in the coil and it’s fastened correctly. | |
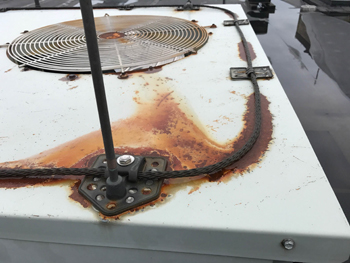 | |
Anyone working with a lightning protection system must be aware of the problems caused by the contact of dissimilar metals, like copper components on an aluminum air conditioning unit. | |
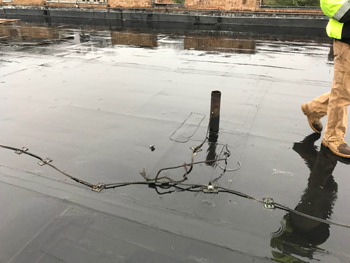 | |
All sorts of problems become possible when lightning protection cables are not properly fastened. | |
 | |
This lightning protection system was apparently “re-installed” after some roofing work, but it was not installed correctly as the cables are not fastened to the roof and the air terminals are incorrectly located. | |
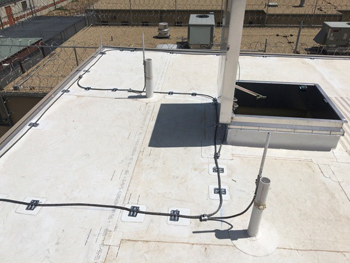 | |
Lightning protection conductors must be securely fastened and bends must be gradual to ensure that the lightning current can travel easily within the lightning protection system. | |
By Jennifer Morgan, Director, East Coast Lightning Equipment Inc.
Torrington, CT - Roofers deal with new challenges on every job. Installing a watertight roofing system requires attention to every detail from exhaust penetrations and skylights to snow retention and gutters.
No matter how good you are at providing your customers with a watertight roofing – or re-roofing – system, installing, connecting and/or disconnecting a lightning protection system is a task better left to specialists.
The greater part of any lightning protection system is actually installed below roof level, requiring plenty of cooperation and communication between those installing the roof, those installing rooftop equipment and the lightning protection systems contractor.
Various components of lightning protection systems are installed before, during and after the roof installation, meaning everyone should be included in the project schedule. Lightning protection system installers are often times one of the first and
last trades on the jobsite.
As with all other aspects of erecting a building there are guidelines and standards that must be followed. Installing a lightning protection system is no different. The National Fire Protection Association (NFPA) publishes a document governing lightning
protection systems: NFPA 780, which is more than 100 pages. It provides lightning protection system installation requirements to safeguard people and property from the risk of fire and related hazards associated with lightning strikes and has specific
requirements for the placement of fasteners, air terminals, conductors and grounding systems.
Those who install metal roofing will be familiar – or should be familiar – with problems caused by the use of dissimilar metals. It’s important to know what metal materials you’re working with to prevent galvanic corrosion. This
is especially true for lightning protection systems, which utilize components constructed from either copper, aluminum or some combination of both metals. When dissimilar metals come into contact with electrolytes, including condensation, rainwater
or other sources such as oil, dirt and airborne particles, it can produce an electrochemical reaction, leading to the corrosion of one or more metals. This can produce staining or even degrade the integrity of the metal itself.
The Lightning Protection Institute (LPI) promotes lightning protection education, awareness and safety, including certifying the installation of lightning protection systems. Underwriters Laboratories (UL) oversees product testing for lightning protection
material components in the factory prior to shipment for listing and labeling. UL Standard 96 addresses the minimum requirements for construction of air terminals, cable conductors, fittings, connectors and fasteners used in lightning protection systems.
UL visits the East Coast Lighting Equipment manufacturing facility
and other production plants quarterly to verify continued compliance.
Since lightning protection systems fall outside the scope of what is typically inspected by local officials, it is common for project specifications to call for a third-party field inspection and certification of the lightning protection system. These
field inspections of completed installations can be arranged by the Lightning Protection Institute – Inspection Program (LPI-IP) through certified installing contractors.
Needless to say, requirements and standards are stringent and necessitate a specific knowledge to install, uninstall or work around a lightning protection system if you want the system to meet standards. Anyone working on the roof also must be sure not
to inadvertently disconnect the lightning protection system, possibly rendering the system nonfunctional or voiding the third-party inspection.
About East Coast Lightning Equipment
Established in 1984, East Coast Lightning Equipment, Inc. (ECLE) provides
high-quality, UL-listed lightning protection system components to lightning protection design and installation contractors throughout the United States, Canada, Central America and the Middle East. ECLE continually strives to develop high-quality,
cost-effective materials that meet or exceed UL and LPI standards for safety. Coupled with a dedication to customer service, this innovative nature has made ECLE a leader in the industry. The family-owned company is based in Connecticut where it manufactures
all of its own products in the United States. To learn more about ECLE, visit www.ecle.biz,
or call (888) 680-9462.
