SAF Implements High-Tech Solution To Improve Aluminum Finishing Process
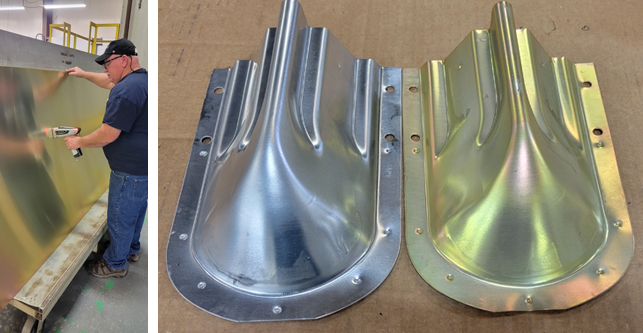
At left, an SAF employee checks the quality of the conversion coating using XRF technology. Fabricators often evaluate the quality of the conversion coating by the changed color of the aluminum. The yellowish piece on the right has been treated. The darker piece on the left has not.
Atlanta, GA — SAF, a global metals distributor, fabricator, and finisher, is substantially improving its ability to confirm the quality of coatings it applies to aluminum, thanks to the introduction of a new tool. The company is now incorporating
X-ray fluorescence spectroscopy (XRF) technology into its polyvinylidene fluoride (PVDF) finishing process. The enhancement enables SAF to provide its customers with verification that its coatings meet key industry standards for performance and durability
set by the American Architectural Manufacturers Association (AAMA).
“In the anodized aluminum industry, there is a saying that your finish is only as good as the aluminum you are anodizing. With PVDF paints, your painted finish is only as good as the pretreatment,” said John McClatchey, vice president of sales
and marketing at SAF. “A real-time XRF measurement provides a more scientific way of measuring the weight of the chromatic film coating on aluminum.”
For a PVDF coating to be properly applied to aluminum, the metal must undergo a chemical bonding process that forms a complex chromate film on its surface, commonly referred to as a conversion coating. Often, fabricators evaluate the quality of this conversion
coating by the color of the metal. However, color does not always correlate with the correct chromatic film coating weight. By using XRF technology, SAF can accurately measure the quality of its conversion coatings. For customers, this ensures an
accurate pretreatment, which leads to a successful PVDF application and a long-lasting architectural finish.
“By using XRF technology, architects, installers, owners, and other stakeholders involved in the construction process know that the finish will last on the aluminum products they are purchasing from SAF,” added McClatchey.
The XRF analyzer works by emitting X-rays and collecting fluorescence radiation from the metal. The test determines whether the metal meets AAMA 2605. With this analyzer, the results are available in seconds as opposed to traditional laboratory testing,
which can take days.
“Today, only a few PVDF applicators are using XRF technology to verify that their aluminum is properly pretreated,” added McClatchey. “It’s another example of how SAF remains on the leading edge of metal finishing for architectural
aluminum.”
About SAF
SAF (Southern Aluminum Finishing Co., Inc.) is a complete resource for metals distribution, finishing, and fabrication.
SAF is a mill-direct buyer of aluminum, aluminum coil and extrusions, as well as a fabricator of ACM systems. To learn more, visit www.saf.com.