By Thomas G. Diamond, P.E., The Garland Company Inc.
If you are reading this article, you likely know how truly beneficial metal can be as a roof or wall covering. Aside from the strength, beauty, aesthetic and geometric design opportunities that it provides, it is 100% recyclable, comprised of a considerable
percentage of recycled content, can provide a wide array of reflectivity, and by design, requires less maintenance than almost any other building enclosure material on the market today.
Metal roofing also carries the lowest cost of ownership over the life of the roof when compared to any other roof system in the industry due to the physical nature of
the metal and the low maintenance costs. Coated steel and aluminum panel systems – if properly designed, installed and maintained – can last for over fifty years. Even more impressive, exotic metals such as zinc, stainless steel and copper
may last well over 100 years. But eventually, that metal will come to the end of its serviceable life. When this time comes, the owner is faced with the decision of whether to retrofit, recoat or replace. Each of these options provides substantial
benefits when utilized in the proper application. But when is it best to retrofit or recoat a metal roof, and what considerations need to be taken into account when making these decisions?
Identifying The Real Issue And Best Course Of Action
Before determining the proper course of action, owners must get to the core of the issue. To do so, ask yourself or the building owner, “What is wrong with the existing roof?” Here are some potential questions to consider:
• Are there only minor leaks or is moisture infiltrating the building throughout the entire facility?
• Is there enough insulation throughout the building envelope?
• Does the old roof still perform well, but look rusted or faded?
• Is there damage to the roof from physical impact, wind, snow, ice, or from age and deterioration?
• Has work been performed on the building that may have damaged the roof, such as mechanical equipment or additions and alterations to the building?
• Does the owner want a new look for their building to upgrade the aesthetic appeal?
Only after truly identifying what is wrong with the roof and what the owner’s expectations are can one make an effective decision on whether to retrofit or recoat. To keep it relatively simple, if the existing roof system is still in good structural
condition but experiences some surface rusting and leaking due to sealant breakdown in seams or poor detailing, retrofitting is likely an effective option. However, if the roof system is still in good condition, only exhibits minor leaks at the seams,
does not contain major rusting or pin hole rusting, but looks to be faded or worn, recoating the roof may be the right course of action. If the existing roof is structurally compromised, exhibits considerable rusting or exhibits large amounts of saturated
insulation beneath the metal roof panels, then the proper course of action is likely to remove the existing roof system and install a new properly designed metal roof. While these basic guidelines are simplistic, every roof deserves a project-specific
review to assess the existing conditions and properly determine the right course of action for the building and for the owner. It is always advisable to consult with an experienced consultant, engineer and/or experienced manufacturer’s representative
to assess the existing conditions and to develop a scope of work that will best suit the building owner’s needs.
Benefits Of Retrofitting An Existing Metal Roof
A metal roof retrofit can provide a vast array of benefits to a building owner. In addition to the time savings that can be achieved without having to tear off the existing metal roof, the facility will typically not need to shut down during the installation
of a retrofit metal roof. Schools, manufacturing facilities and food processing plants, to name a few, can experience detrimental monetary and operational effects if a shutdown is required to install a new roof.
Without having to remove the existing panels, retrofitting also reduces the overall labor cost of the project. The true benefit of this, aside from saving money on the initial installation, is the opportunity to reallocate that saved capital on a high
performance standing seam metal roof system. These systems, when designed and installed correctly, typically require less maintenance and last longer than through-fastened metal panel systems, lowering the overall cost of ownership throughout the
life of the roof.
Some older metal buildings may also be lacking in their insulation package within the roof assembly. More recent versions of energy code, such as the International Energy Conservation Code, are increasing prescribed R-value requirements. A retrofit provides
the opportunity to increase the roof assembly R-value in accordance with code requirements, while simultaneously increasing energy efficiency and the comfort level of the building inhabitants. If existing batt insulation beneath the panels is saturated
or falling apart, the best option during a retrofit is typically to remove the old insulation and install the new, code-required amount of insulation on top of the old roof panels and beneath the new.
Metal Retrofit Methods And Considerations
Section 1511.3.1 of the 2015 International Building Code (IBC) states, “The installation of a new roof over an existing roof covering shall be permitted where any of the following conditions occur:”1 The second permissible condition
is “Complete and separate roofing systems, such as standing-seam metal roof panel systems, that are designed to transmit the roof load directly to the building’s structural system and that do not rely on existing roofs and roof coverings
for support, shall not require the removal of the existing roof coverings.”1 However, a licensed structural engineer should be consulted on every retrofit project. The engineer should perform a structural evaluation to assure that
the existing roof structure can withstand the additional dead load of the retrofit framing and the new metal roof. This is an especially critical step to take on pre-engineered metal buildings where there may not be enough capacity for additional
dead loads.
The most common way to retrofit an existing metal roof is to utilize structural framing members that fasten through the existing panel and into the framing of the roof
structure. By doing this, the additional load of the new roof is transferred to the structure as opposed to the existing metal panel. The framing is typically comprised of 14- or 16-gauge steel, but may be thicker as required on a project-to-project
basis. Notches are commonly cut into the bottom of these framing members to allow them to conform to the ribs or seams of an existing metal roof. As a temporary waterproofing measure, sealant should be applied to the head of all fasteners that are
used to attach the framing, as they may remain exposed for an extended period of time prior to the installation of the roof panels. Additional insulation, if needed, can then be laid between the new framing members prior to the installation of the
panels.
A structural engineer can also design the height, thickness, spacing and attachment rate of the retrofit framing. The spacing of the existing roof structure’s purlins typically dictate the spacing of the new framing system, but this needs to be
individually checked and designed for each and every project. The manufacturer of the new metal roof should provide the attachment requirements of the panel to the framing using wind uplift resistance testing in accordance with the ASTM E1592 or FM
4474 test standards, as required by IBC. A structural engineer can also be contracted to assure the attachment of the new metal roof is sufficient, using the manufacturer’s test data and recommendations.
Another method of retrofitting an existing metal roof is to overlay a single-ply or light gauge through-fastened metal panel. This style of retrofit is typically addressed by filling the flutes of the existing roof with insulation, cut to conform to the
shape of the existing panel. The single-ply system or metal system is then fastened to either the existing panel or to a framing system that is attached to the structure of the building. The method of attachment should be designed in accordance with
manufacturer’s guidelines and should be engineered for each project as there may be structural concerns, such as weight and wind uplift resistance, that need to be addressed with the existing roof. In these applications, roof pitch should be
limited to 1:12 or greater, or per manufacturer’s requirements. Slopes that are lower than this may not allow for positive drainage behind seams, which can lead to premature breakdown of the seams and maintenance concerns. Even though this method
provides a lightweight solution to retrofitting, weight is still being added to the roof. Therefore, a structural evaluation should be performed to assure the dead load capacity of the roof is not exceeded. Modified bituminous membrane roof systems
may also be considered for retrofit applications, but this option comes with a relatively large amount of added weight which is usually not practical and cannot be accomplished without exceeding the dead load capacity of the existing roof structure.
Additional considerations that need to be taken into account are flashing components, which should be a minimum of eight inches in height. Mechanical units, vents, wall flashings, etc. may need to be raised in order to achieve the eight-inch height. This
may add unaccounted cost to the project if it is not addressed during the design phase. If ventilation is present in the existing metal roof, it must also be carried through into the new metal roof. Failure to do so may result in building envelope
performance issues such as condensation.
Recoating An Existing Metal Roof
 |
Before (above) and after (below) recoating. |
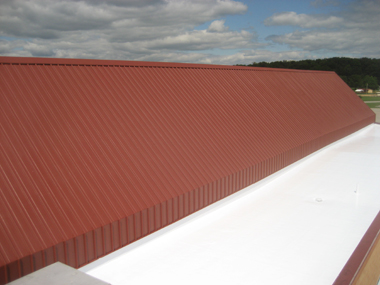 |
When the existing roof system still performs well and is structurally sound but exhibits minor wear and tear at the seams or the finish looks faded, surface rusted, worn or just needs updated, a recoat of the existing metal roof may be the right solution.
A new coating can provide a beautiful new appearance to a facility at a much lower cost than a retrofit. However, before choosing this option be aware of the surrounding conditions of the building that may have caused the issues to begin with. If
the existing roof is leaking due to poor detail designs, additions to the roof, or a low-grade metal roof panel, recoating the roof will not solve these issues. Additionally, if the existing finish is staining, fading, flaking or rusting due to chemical
or abnormal atmospheric conditions, or if the existing paint is damaged due to physical abuse, recoating – or recoating with the wrong type of system – will likely lead to another premature failure of the panel’s finish.
When a recoating is chosen as the right solution, there are a number of considerations to take into account. In order to determine which coating is best, the conditions of the existing substrate need to be assessed by a coating manufacturer or experienced
applicator. There is a vast array of finish and coating options available in the market today. Some options include:
• Field applied fluorocarbon paint finishes
• Acrylic or acrylic latex finishes
• Asphaltic coatings
• Solvent-based urethane coatings
• Silicone coatings
• Solvent-based rubber coatings
• Thermoplastic coatings
An experienced high-performance manufacturer should be able to assess the existing substrate’s conditions, chose the applicable product options for the project and determine the preparation required for the system.
As any coating manufacturer or experienced applicator will tell you, preparation is the most critical component of a recoating project. The preparation required for a recoating project can be just as expensive as the labor required for a retrofit project.
However, the cost of materials for a recoat will likely be far less than that of a retrofit, making the recoat project more cost effective. Some common preparation conditions and techniques include:
• Solvent cleaning for the removal of grease, oil, dirt or other soluble contaminants
• Hand tool cleaning such as chipping sanding or brushing for the removal of loose rust, mill scale, loose paint or other foreign matter
• Power tool cleaning for a more aggressive removal of the substances mentioned above
• Pressure washing
• High-pressure water jetting
• Blast cleaning
The Society for Protective Coatings (SSPC) provides surface preparation standards that can be used as guidelines for proper surface preparation techniques and requirements.2 However, as stated previously, it is critical to consult with a coating
manufacturer and experienced applicator to determine which products and surface preparation techniques will be required for each and every project.
Conclusion
There are a variety of options available when it comes to determining what to do with an existing metal roof that may be near the end of its serviceable life. Retrofitting it with a new high-performance metal roof can provide decades of protection and
beauty. Recoating the system – if conditions allow for it –provides an aesthetic upgrade that may also allow the roof to continue to perform for many years. Either option must be addressed on a project-to-project basis and should be done
so with the help of an experienced industry professional or manufacturer’s representative to help avoid potential pitfalls that could be more costly than anticipated. But when the right course of action is determined, and the right product,
design, preparation, installation and maintenance plan are employed, the solution will afford a building owner time and money to focus on their business as opposed to the roof that protects it.
References:
1 IBC, 2015 International Building Code
2 SSPC, Society of Protective Coatings, Surface Preparation Standard