By Scott Moffatt, PPG
Metal coatings have come a long way. Not only have their protective and environmental qualities improved dramatically in recent years, but so have the range of colors and effects now available.
Thanks to these new innovations and technologies, architects can choose from an extraordinary palette of decorative colors and special effects for commercial office buildings, retail stores and entertainment complexes.
While these developments are overwhelmingly positive, they also have heightened the need for more vigilant color-matching and quality control measures on the part of coatings applicators and their customers. As the number of coatings, colors and special
effects have expanded, so have opportunities for color variation. Even subtle differences in color, which may look negligible when building components arrive on a job site, can be exaggerated when components are installed on a building.
This article is the first in a series of five intended to help architects and other building professionals more effectively color-match architectural metal coatings so that:
1. Building components arrive on the job site coated in the colors specified; and
2. Components produced by different coatings applicators appear as a coordinated whole when installed together on a building.
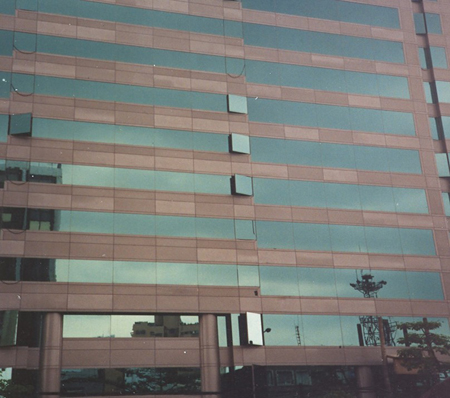 |
Small variations throughout the coatings process can accumulate, producing noticeable color differences among coated building components. When installed on a building, these mismatched components may demonstrate a checkerboard effect. |
Avoiding the Checkboard Effect
A new generation of coatings, incorporating natural materials such as metallics and micas, has helped contemporary architects create some truly extraordinary buildings. Unfortunately, coordinating coatings across numerous building components can present
difficulties that prevent architects from achieving their intended vision.
In most instances, the differences between the architect’s original vision and the finished coatings on a building are minimal. In extreme cases, however, small variations throughout the coatings process — from concept to finished product
— can accumulate. This produces noticeable and unacceptable color differences among coated building components. When installed on a building, these mismatched components may demonstrate a “checkerboard effect”.
These problems often can be traced directly to the original color specification. To minimize color-matching problems, architects and specifiers should practice these five principles when evaluating color at the specification phase:
1. Colors chosen for an individual project are usually selected from a collection of printed chips or samples, then viewed in lighting conditions different from those in the field. To achieve the truest match, color samples should be viewed in the environment
of the coating’s finished setting and at the angle at which the coating will be placed, typically a vertical orientation.
2. Time of day and time of year can also affect the appearance of individual colors. Natural light is neither uniform nor constant, and its characteristics also will vary according to atmospheric conditions.
3. The height, angle or distance from a light source also can alter the appearance of a color, as can its surrounding environment. The color on a building surrounded by trees will look different next to an open landscape, an interstate highway or another
collection of buildings.
4. This also is true of certain solid colors, micas and metallics, which can reflect different appearances according to the surrounding light and the orientation of individual flakes.
5. Finally, consider the gloss and the surface character of the sample chip itself. One coatings manufacturer may provide coating samples on galvanized steel substrate, while another may apply their coatings to an aluminum substrate. To ensure the truest
color representation, insist that color samples be coated on the actual substrate from which the building panel or extrusion will be manufactured.
The second article in this series will explain how to manage color variation when multiple coating applicators and/or coating methods are working on a single project.