By John Pierson, PE, The Garland Co. Inc.
A low-slope roof is the most abused surface on a building. Mother Nature is tough on building exteriors in general, but low-slope roofs – or flat roofs – take the worst of it. Sun exposure is more intense; wind develops higher uplift pressures making them more susceptible to blow off; rain, snow, and ice accumulate causing damage; dirt and debris can build up and clog drains; and people walk on them without much regard to their impact on the roof system. If this sounds familiar, you might consider a retrofit metal roof framing system.
| |
| A typical retrofit metal roof and framing system. |
Increasing the slope of a roof with steel framing and standing seam metal roof panels has been in practice for a long time. Today’s building owners can benefit from decades of experience with these systems and time-tested solutions. With that in mind, here are some important points that anyone considering a metal retrofit should review.
Retrofit metal roofing systems require a significant amount of planning. Changing the appearance of the building with a retrofit system may also require significant changes to other building systems, which may involve several different professional disciplines. It is important to work with a partner that is capable of providing all the services necessary with responsibility that carries from design through the installation of the system. Design criteria that should be addressed include the following:
Roof Panel Design
The standing seam roof panel must be designed to meet the slope, geometry, and design loads of the proposed project. All too often, a great deal of time and energy is spent on designing a proper retrofit framing system, then little effort, outside of a structural loading check, goes into design of the metal roof panel. There are strong structural standing seam panels available which have outstanding water proofing characteristics. Design decisions need to be made and specified clearly to include them.
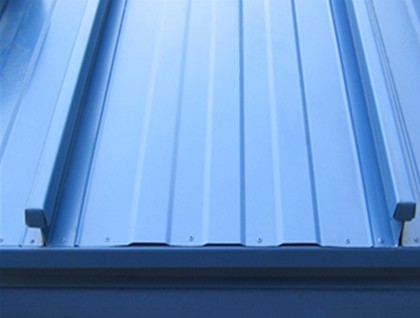 | |
High-performance structural and watertight standing seam metal roof. | |
Warranties are a good starting point for guidance on watertight capabilities, but more important is the product testing specific to water tightness. Here are a few tests that should be used to gauge the long term water tightness of standing seam panels:
• Daily Weather Exposure (20.0 psf): ASTM E 1646 Standard Test Method for Water Penetration of Exterior Metal Roof Panel Systems
• Long Term Seam Sealant Performance Under Cyclic Loading (20.0 psf): ASTM E 1680 Standard Test Method for Rate of Air Leakage Through Exterior Metal Roof Panel Systems
• Wind Driven Rain (35 to 110 mph): TAS 100 Test Procedure for Wind and Wind Driven Rain Resistance of Discontinuous Roof Systems
• Product Submersion Evaluation: ASTM E 2140 Standard Test Method for Water Penetration of Metal Roof Panel Systems By Static Water Pressure Head
These tests cover more severe, but common weather including wind driven rain at storm measured wind speeds.
In the eyes of a metal roofer, most of the retrofit framing applications are relatively low slope, which is to say 3:12 or less. For this application, a standing seam metal roof should meet the following design criteria:
• Watertight on slopes as low as ¼:12
• Factory installed seam sealants which are isolated from attachment clips where it can be damaged from thermal movement
• Unlimited thermal movement at the anchor clip locations.
• Transitions and terminations should be sealed with a combination of metal backed foam closures and tripolymer, fluorocarbon paint compatible sealants.
• No through fasteners. Screws and/or pop rivets should only be used to make structural connections outside the plane of waterproofing.
Analyzing The Existing Building
| |
| Solar installation over a retrofit metal roof. |
A framing system is engineered to seamlessly integrate with the existing building structure. While the light-gauge steel and sheet metal used for these roofing systems is relatively light, it can double the weight of the existing roof. The weight of the average retrofit framing system and the metal roof panels are typically about 3 to 4 pounds per square foot, installed. For steel deck roof assemblies this represents an increase in dead load more than 5%, triggering a structural analysis according to International Building Code Requirements.
Most decking is not designed for the point loads imposed by the vertical members used in these framing systems. Tributary areas are typically in excess of 32 square feet so controlling wind uplift forces can exceed 2,500 lbs. at connection points. In metal, wood, or composite decking, connections must be made to the steel structure below the deck. Concrete decks may be suitable if they are assessed to have adequate strength.
A structural evaluation should be performed to determine whether the roof structure can support the additional weight. So, the structural evaluation is very much a feasibility study to see if retrofit framing is a viable option. What it also provides is a way to check the options for anchoring the proposed framing system, the geometry limitations in the architecture of the new roof, and other building envelope concerns such as rooftop mechanical and utilities, storm water drainage, insulation, and moisture control.
Energy Efficiency
Adding insulation in the newly created attic space can help with the energy efficiency of the building. By adding an attic space to the equation, the energy code requirements change. Roof insulation on a low slope is referenced as “insulation entirely above deck” whereas “attic and other” is significantly higher. However, a prudent designer can rely on the maximum U-factor method to determine a value for the entire assembly. A thorough condition assessment of the existing roof is critical to determine the best opportunities to maximize insulation value. Fiberglass insulation is the most economical option, but it should only be used if a proper air barrier is in place.
Air barriers are now required by energy code in our new buildings. The retrofit roof offers the same opportunity to save energy through reducing air leakage. It also provides a means to reduce condensation related moisture problems. Condensation concerns are a close second to waterproofing. A vapor retarding air barrier is usually a necessary component in metal retrofit roof systems.
| |
Retrofit metal roof with insulation and air barrier. | |
Creating proper ventilation under the new roof is important for the energy conservation also. Passive ventilation is only acceptable if you can create suitable soffit to ridge venting. Venting plays an important role in the architecture of the new roof such as deciding on soffit width or using hipped ridge lines instead of gable end walls. Approximately 30 percent of soffit and ridge space should be open for passive ventilation to meet minimum requirements. If powered ventilation is selected, it must be designed appropriately to work effectively and efficiently so conditioned air is not drawn from inside the building, resulting in a negative energy impact.
Architectural Considerations
Not every roof is right for retrofit. With all of the benefits metal retrofit systems provide it is important not to lose sight of the primary reason, which is to provide waterproofing protection. One of the biggest considerations in determining whether a retrofit will work is the existing layout of the building, including slope and building geometry.
| |
| New retrofit metal roof with replacement low-slope roof area. |
A combination of retrofit metal with low slope areas is often a good solution for buildings that were not originally designed with sloping roof lines. This should not cause distress as low slope systems with performance and life expectancy similar to metal roof systems (30 to 40 years) are available. Using low slope materials in conjunction with retrofit metal does not have to be tricky or difficult; it is done quite often and experienced professionals can guide the process. It is important to consider the warranty impact of how these materials are specified because the tie-in details where these systems meet are often a no-man’s-land of responsibility. Ensure your details and specification address each detail properly.
This article highlighted a few of the most important points when considering a metal retrofit, but there are many more details which need to be sorted out including local building code checks, fire safety, and construction considerations, just to name a few.
Success of your next project depends on expert knowledge of these specialty roofing applications. Seek out industry professionals who can build a team with necessary design experience, proven product performance, and quality installation.