By Jeff Alexander, Valspar Corporation
Nowadays, coatings come in nearly every color imaginable, not to mention new aesthetic treatments. Manufacturers are able to create patterns, textures and color-shifting finishes that provide architects with a diverse portfolio to select a product from for their next masterpiece. However, a superior coating will go further than just achieving a desired aesthetic – it will increase the durability of a structure, as well, and provide expert resistance to harmful elements in high-stress environments. When considering how to protect against harsh weather conditions, be sure to consider both metal building product location as well as coating composition.
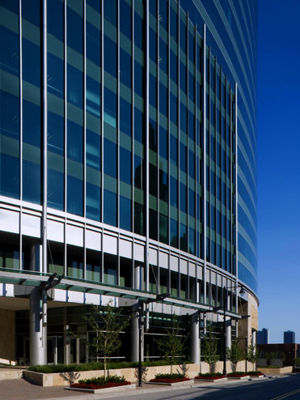 | 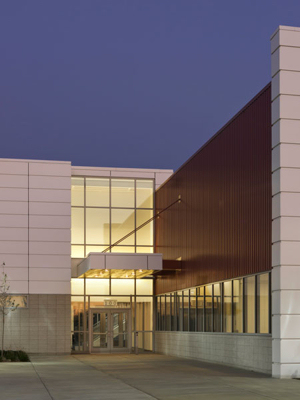 |
There's no such thing as a typical metal construction project these days, with metal claddings used as commonly on modern commercial claddings as they are on traditional metal buildings. |
Building Location
Mother Nature knows no bounds and her wrath can be devastating to infrastructure. The good thing is, you have options for protection against the elements in any environment when it comes to coatings. Manufacturers understand that you have many things to consider, like the damaging effects of sunlight and harsh rays on a building, depending on the location of the metal building product. To address these concerns, as well as cost, coatings are composed with different resins.
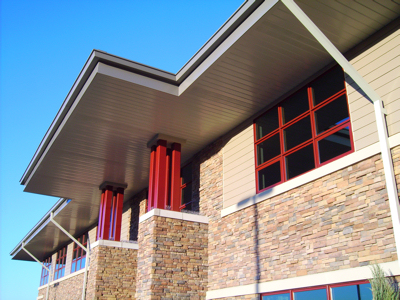 |
No matter the project or metal construction product, chances are there's a paint finish designed just for it. Metal construction product representatives are well-versed on the differences in coatings and can generally recommend the best product for the given parameters. For more unusual needs - something special - it's often best to include the coating manufacturer in the discussion. |
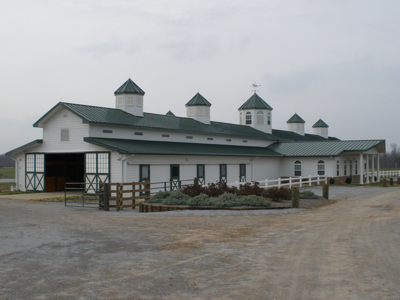 |
Coating Composition
Resins serve as the binder that forms the paint film and determines the durability, appearance and performance of the coating, in addition to the level of weather-resistance. Different coatings contain different formulations and some are better suited for specific applications than others.
• Polyester: Polyester resins are known for their flexibility and adhesion properties. A more cost effective coating, you can expect outstanding color consistency and resistance to dirt and stains, however they are best used in areas that will not see full sun, like gutter systems or interior metal cladding.
• Silicone-Modified Polyester: The next step up in resistance, silicone-modified polyester coatings are heralded for their tremendous gloss retention and ability to stand up to harsher weather conditions. These coatings, which are a great choice for metal roof and wall panels, offer a better resistance to UV-rays, while still protecting against abrasions, chipping and marring.
• PVDF (Polyvinylidene Fluoride): The most widely known resin in the coating industry, PVDF-based finishes provide high levels of resistance to weathering, chalking and marring. If you are looking for extreme durability and weather resistance, look for a coating with a high-percentage PVDF resin. For instance, a 70 percent PVDF coating blended with an acrylic resin will stand up to full sun exposure without sacrificing aesthetic. PVDF coatings are widely used, not only on metal roof and wall panels, but on framing for curtain walls, windows, skylights and entrance systems, louvers and grills, soffits, fascia and mullions.
Coating manufacturers know their products are more than just the color. Creating durable coatings is an essential facet of the formulation process. R&D teams across the globe strive to maintain the benefits of their flagship coating lines while also increasing durability and resistance properties. As you look around to find the best fit for your next project, be mindful that a coating can provide durability and sustainability as well as contributing to the ultimate colorful design aesthetic.