By Jaswinder Bhatti, Samco Machinery
When researching to purchase a one-of-a-kind roll former, the more information you bring to the manufacturer, the better your chances of getting a roll former that does what you need it to do.
Purchasing a custom roll former is one of your business’s larger investments. Getting the most out of your investment depends on designing a machine that will produce consistent product for a long time. The design will only be as good as the information provided to the roll former manufacturer so it’s important to have all the questions answered and every consideration covered.
Not only will quality roll former manufacturers be able to take the information provided by the customer and design a machine capable of producing the desired part, they will ask for and seek out information the customer may not have realized was necessary. The roll former manufacturer should be the expert on roll forming.
 | |
Double Duplex Thru Shaft – Described by the author as a must when profiles required have variable flange heights and widths, such as metal studs and purlin products. | |
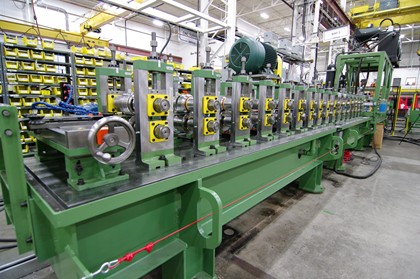 | |
Universal SUB (Non-Rafted) – General purpose all-around use roll former. | |
 | |
Universal SUB (Rafted) – Can produce many different profiles with a simple change of rafts. Suitable for roof decks and panel profiles. | |
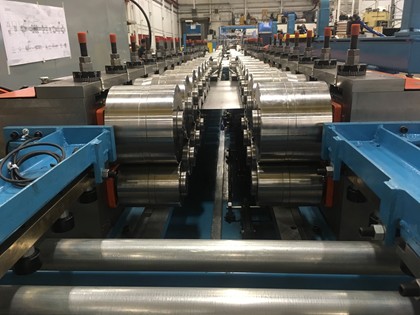 | |
Stub Shaft – The author calls this a perfect machine for edge forming variable width profiles. | |
What follows is a list covering many of the considerations a roll former manufacturer will look at during the machine design process.
Machine Usage
The manufacturer will straight away want to determine if this is a general purpose machine (making multiple profiles) or one dedicated to producing a selected profile.
Material Thickness
The thickness of the material being formed will help determine the size of the machine as well as the shaft diameter sizing. Generally, a thicker material will require a longer machine with more stations and a larger shaft diameter.
Certain materials may have a need for a lubrication station at the entry, requiring a longer machine as well as more space for the machine once it’s up and running in a plant.
Type Of Material
Every material will react differently to the stress of roll forming. Some materials are more malleable, or softer, than others. Softer materials may require fewer bending stations.
Black steel, galvanized steel, prepainted steel, stainless steel, aluminum, copper, brass…all react differently to the roll forming process. Experienced roll former manufacturers will know these characteristics and provide the best design accordingly.
Yield Strength Of Material
Yield strength of any material going through a roll forming process is another important consideration during the design process of a roll former. Yield strength will help determine machine sizing, the degree of a bend per station as well as the number of stations required to create the desired part.
Steel companies are producing steel with increased yield strength. Thirty years ago, the yield strength of high-yield steel was 50 ksi. Today, it’s 220 ksi, which makes for a whole new ballgame when determining the number of stations and the maximum degree of bending the material will require.
Elongation Of Material
When the yield strength of high-yield steel was 50 ksi, the elongation was 22 percent. With today’s 220 ksi, it drops to only 3 percent, so calculations are totally different than they were in the 1980’s. Running a machine too slow or too fast could damage material. So could bending material too much in a given station.
The higher yield strength will also require a different calculation involving over-bending. Bend radii must be calculated based on yield strength and elongation.
Number Of Bends
During the design process, calculations involving the number of bends will be determined. This will help determine the number of bending stations, the tooling design, as well as what drive system is required.
Total Degree Of Bends
Another part of the design process is determining the total degree of bends required to form the desired part from flat steel. This affects the number of stations and therefore, machine sizing, as well as tooling design.
The total degree of bends will also help determine the motor size required to match the desired speed of the roll former.
Height Of Section
Simply, the height of the product determines the height of the section it’s passing through. Different stations may require different heights to accommodate a changing shape during the roll forming process. Horizontal and vertical distance of stands is determined based on the section height.
Volume Of Production
This information is critical. Generally affecting the drive, but product configuration is critical in determining the requirement. Generally referred to in terms of feet per minute but ultimately calculated in lineal feet per day.
Width Of Section
The width of the section being formed helps determine the length and size of the shaft. If a 36-inch wide piece of material is going through the machine and the center of the material is being formed, a bigger shaft diameter is required. If the outer edges of the material are being formed, a smaller shaft diameter could be selected.
Pre-Cut Or Post-Cut
Generally the pre-cut vs. post cut decision is best left to the manufacturer of the roll former. Some shapes perform a lot better when post-cut to suit the accompanying technology required to achieve those results. Deep roof deck profiles should be post-cut to avoid “spring back” or flare inherent in deep profiles. Automotive parts, due to their tight tolerance requirements formed with high-strength steels, are almost exclusively run in a post-cut manner.
Pre-cut parts eliminate cut-off dies and their maintenance, but create the possibility of end flare, especially in deeper parts. The production rate is higher with post-cut parts and there is better quality control of parts.
Pre-Punched Holes Or Post-Punched Holes
The determining factor here is where the holes fall in relationship to bends. If holes are near bends and could be elongated or have their shape affected by the roll forming process, parts should be post-punched if possible. Or, the number of passes may have to be increased to accommodate the holes closer to the bend area.
For post-punching, make sure the areas that need to be punched can be reached by the punching device after the bends.
Profile Tolerance
Profile tolerance and number of bends will affect the number of stations required in the roll forming process. It will then also affect the size of the machine.
The bottom line is, the more information the machinery manufacturer is supplied with, the better the result will be.