By Paul Collyer, Vice President of Business Development, Metl-Span
Insulated metal panels (IMPs) can be installed either vertically or horizontally. With most manufacturers’ wall panels, the exact same panels are used for either orientation. However, there are key differences in how the supporting wall system must be designed to accommodate the panel direction. In addition, the details used to design and the labor used to install vertical vs. horizontal panels can be quite different. Let’s explore some of the similarities and differences in the two approaches.
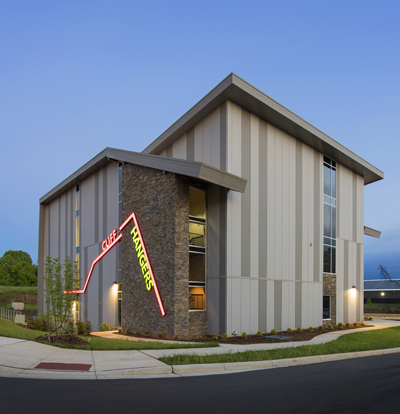 |
|
Shown above are two recent projects involving the use of vertically installed insulated metal panel systems from Metl-Span. The projects below show Metl-Span systems installed in a horizontal fashion. Click on the images to read about each job. |
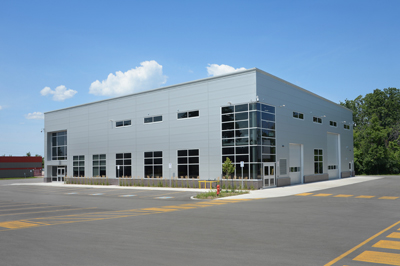 |
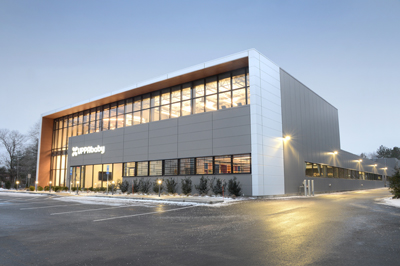 |
Vertical IMP applications
Vertically installed panels typically offer the most cost-effective and simple wall assembly. There are numerous panels available in lengths of up to 52 feet, offering the ability to install a single panel from base to eaves.
When laying out the panels on a wall, the starting panel at the corner can be cut along its length so the first and last panel on a wall elevation are equal in size (width). Standard metal flashings are generally used to close off the cut ends and edges of vertical panels.
Windows are usually installed to align with the outside plane of the structural framing and are therefore recessed (not flush) relative to the outside face of the panel. Typical wall framing systems for vertically installed panels involve the use of horizontal supports, usually light or heavy gauge girts.
Horizontal IMP Applications
Horizontally installed panels require more sophisticated details and tighter tolerances for both panels and framing. Panels are usually arranged so the ends of the panels align with architectural features, such as framed openings for windows and doors. Corners are often built with factory-folded transverse bent panels, shipped to the jobsite ready to install.
The vertical ends of horizontal panels are often post-fabricated with trimless ends. This involves manufacturing the exterior panel face longer than the interior face of the panel, providing extra metal at the ends that can be bent back at a 90-degree angle. This trimless end is an efficient and attractive way to cover the exposed foam core at the ends of the panels.
Some companies offer an integrated window system that fits directly into the panel’s joinery, allowing them to be installed to provide a flush window system. That along with the exterior panel faces improves continuity of building control layers. Horizontal panels also require a vertical support system, which is generally comprised of a steel stud wall assembly or occasionally a vertical tube steel system.
When using horizontal panels, it is also generally necessary to use thicker (22 gauge) exterior faces to achieve satisfactory aesthetic performance, particularly when using flat or nearly flat panel profiles. Thicker gauges tend to stiffen the metal and provide a visually flatter appearance than lighter gauges, greatly reducing the tendency for oil-canning (waviness). Also, it is important to keep horizontal panels shorter (usually no more than 20 feet in length) than those used in a vertical orientation. This is because the casual observer tends to detect more visual flaws when looking along the length of horizontal panels than looking up and down vertical panels.