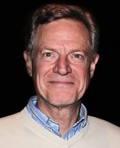
By Scott Moffatt, PPG
This article is the second in a series of five intended to help architects and other building professionals more effectively match colors on architectural metal coatings so that:
1. Building components arrive on the job site coated in the colors specified; and
2. Components produced by different coatings applicators appear as a coordinated whole when installed together on a building.
The first article covered offered five rules for proper color-matching at the specification phase. This one provides color management tips for projects with multiple coatings applicators and application methods.
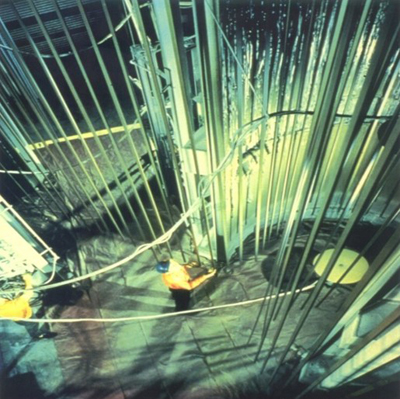 |
Different application methods can result in major differences in final color appearance. |
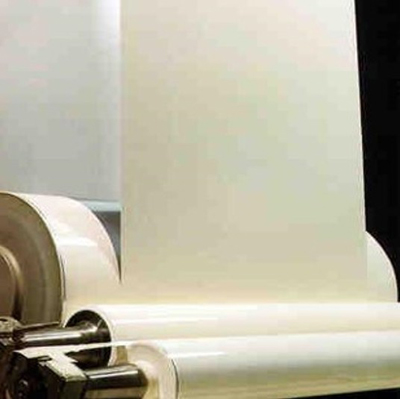
|
Coil coatings are usually applied at lower film rates than spray coatings. |
Color Standards and Color Control
Color-matching problems are common when multiple coating applicators are used on a project. American Architectural Manufacturers Association (AAMA) standards require that multiple applicators submitting coatings of the same color for the same part of
a building measure within two Delta E units (DE) of one another on the Hunter color scale.
The methods of spray-applying paint and the equipment used to do so can cause the same coating color to vary widely from one applicator to the next. For instance, all coatings applicators apply material on vertical or horizontal paint lines utilizing
different application equipment. Reciprocating discs are used on vertical lines, and bells or spray guns on horizontal paint systems. These distinguishing factors — along with the target distance from the paint equipment to the part that is
being coated — determine how the color is formed. Individually or taken together, each of these elements can produce significant color differences across different coating lines.
Another variable is coil coating versus spray applications. The coil coating process produces colors that look different than extrusion coatings based on the application method. Coil coatings are roll-coated while aluminum extrusions and other components
are spray-coated. Consistent solid colors are much easier to produce than consistent special-effect colors, as micas and metallics orient differently in special-effect paint films, producing greater variation in visual reflectance and color.
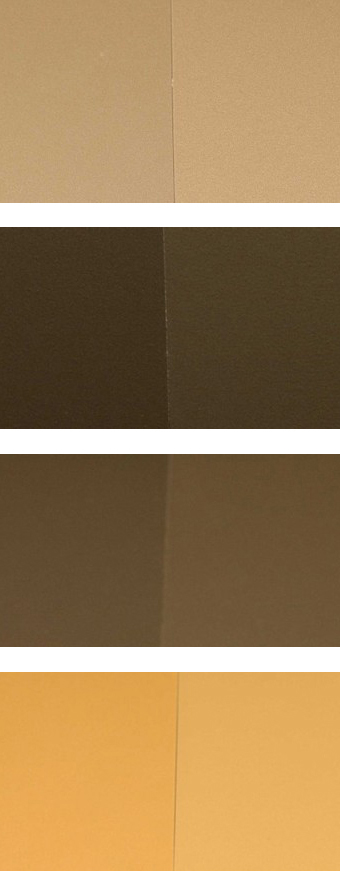 |
The images shown above illustrate extreme color differences among panels finished with the same batch of paint applied by different applications methods. |
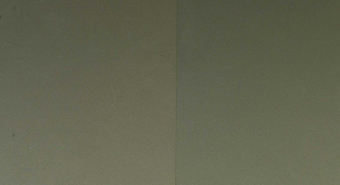 |
This image above illustrates the color differences that can be created by coatings applicators using different spray application methods. |
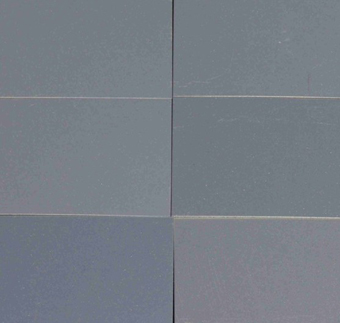 |
These panels demonstrate the potential impact of applying the same paint at different times. |
Operating conditions at the time of manufacture also can affect a coating’s final appearance. Temperature, humidity, the curing process and how thick the coating is applied are variables that can fluctuate daily, even within the same plant. Color differences can also be attributed to the line operator.
To minimize the potential color differences related to these variables, architects and contractors should adhere to the following guidelines:
1. Limit the number of coatings applicators used on each project. Lessening the number of suppliers reduces the chances for color-matching and quality problems.
2. Once coatings applicators have been identified, notify the coatings manufacturer of who will be responsible for which building components. This will facilitate better color coordination among the different applicators.
3. Use the primary applicator panel as the standard. That way, the coatings manufacturer can make sure the standards for each coatings applicator match one another. Note: Do not use coil coating standards for spray coatings or vice versa. Each application method should have its own individual standard.
4. For large projects, request color standards from each coatings applicator. Use the standards to determine the capabilities of each applicator and apply that knowledge to more effectively manage the color-matching/coordination process.
5. Adjust the color match on coil coatings to the color of the spray coatings. Color control is more exact with coil coatings than with spray coatings. That means it is easier to establish a color standard with a spray coating then formulate the coil
standard to match it. The only exception to this rule is for white or light-colored coatings. In these cases, the coil coating should be used as the template since coil coatings are usually applied at a thinner film rate (which makes them more difficult
to adjust).
The third article in this series will identify three key color control variables for matching architectural components on a single project.