By Dale Nelson, Roof Hugger, LLC
Hurricane Ian has provided us with yet another stark reminder of the importance of the strength of your building and, in particular, your roof. The upgrades from older buildings to today’s are quite dramatic, especially in the high wind regions of
our country.
Prior to 2000 and the adoption of the International Building Code (IBC), building roofs were designed based on uniform or equal loading across the entire roof. For example, an 80' wide x 100' long x 22' eave height building, in Tampa, FL, would have a
wind speed design of 110 mph and loading of about -20 lbs./psf. over the whole roof. After 2000 and the more universal adoption of ASCE-7 and the IBC code, roofs were more accurately divided into “zones”. (I) Roof field, (II) edge zones
and (III) corner zones were created. The latest version of the 2021 IBC code has added even more roof zones.
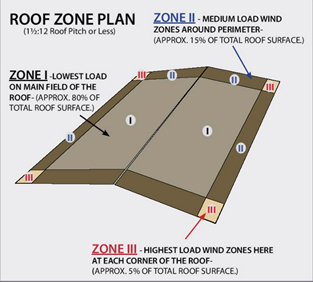 |
Figure 1: Roof Zone ASCE7 - 10 |
Each zone has its own design loading for uplift; the corners would be the highest loading, edges next highest and field the lowest. That same 80' x 100' x 22' building in 2022 now uses 141 mph wind speed, roof loads are now -34psf in the field, -45psf
in the edges and -62psf in the corners...3x the original design. If this building was located in an open terrain area, the corner zone loads would increase to over -80psf. This is a jump of 4x the original load design for older buildings.
The good news is that it is possible to retrofit almost any older building and bring it to the current IBC design requirements. Like all re-roofing however, retrofitting can be expensive.
Metal roofing is a premium long-life product, so what if your old metal roof is still in ok shape and you do not have the cost of a retrofit roof in the budget at this time? There are a few things you can do to make your existing roof stronger, giving
your building and its contents a better chance of surviving an extreme storm event.
Will these changes allow you to meet the current code? Probably not, but your old code roof will certainly be stronger than it is currently.
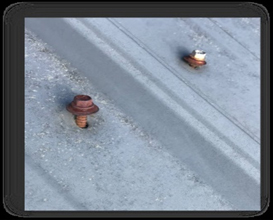 |
Figure 2: Failed/Loose Fasteners |
Many older roofs are the through-fastened or screw-down type roofs. First, inspect the old fasteners, replace any corroded or loose fasteners with quality, oversize stainless steel or zinc alloy, weather guard fasteners – these small fasteners are
a critical part of your building; they not only hold your roof down to the structure but they transfer the diaphragm strength of the roof panels to the roof framing, giving it needed structural rigidity.
The most common metal roof panel is the 12” o.c. ribbed “PBR” panels. These panels are typically attached with 1 fastener every 12”.
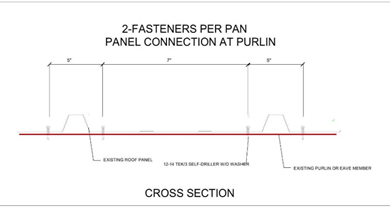 |
Figure 3: 2-Fastener/L.F. Attachment Pattern |
It’s hard to believe but adding just 1 additional fastener to the panel every 12” for a total of 2 fasteners per L.F. in zones II & III, (Typically 5’-10’ in from the eave and rake of the building) will increase the strength
dramatically. The design capacity of a typical “R” panel in these areas could increase from approximately -45 lbs./psf to around -60 lbs./psf. Assuming 5’ purlin spacing, this one additional fastener can improve roof panel design
capacity by 33% or more. It is also important to note this increase is in design capacity. Metal roof panel design capacity is typically determined after a factor of safety of 2.0 is applied meaning, theoretically, they have more capacity before predicted
failure.
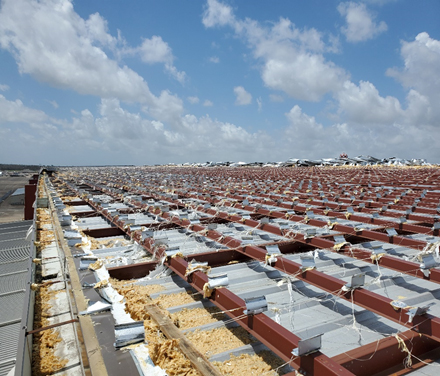 |
Figure 4: Failed Roof Panels |
The next thing to look at is the building's rake trim. That is the trim piece on the gable end of the building at the top of the end wall that covers the side edges of the roof panels.
Most roof failures begin at the corners or rake edges of the building. If the trim comes off, the edges of the panels become exposed to the harsh pressure of the wind. This applies to the wall corner trim as well. I prefer these trim fasteners to be no
more than 12” o.c.
Finally check the gutter attachment and make sure the straps and attachment fasteners are not corroded and weak; replace them as needed. They are typically spaced about 3’-0” o.c.
OK, but what can you do if you have a standing seam roof, not a screw-down roof? Adding fasteners to a standing seam roof defeats the whole reason to have one because standing seam roof panels need to be allowed to move with expansion and contraction.
High strength sliding clips are seamed into the roof panel side-laps and have the ability to hold the panels firmly down and still slide as the panels move with heating and cooling.
The capacity of these panels is in large part controlled by the clips that hold the panels. A common mode of failure is the panels detaching from the panel clips. It is possible, however, to increase the holding power of these floating clips by adding
external “Wind Clamps” or “External Seam Clamps”. These clamps are installed on top of the roof panels seams at the attachment clips. They do not penetrate the panels nor do they impede the movement of the panel, but they greatly
increase the holding power of the panel to the clips.
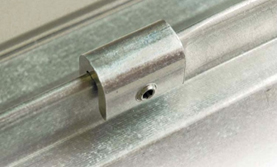 |
Figure 5: Courtesy S-5! |
A typical 24” standing seam panel on 5’ purlins may have a design capacity of -35 to -40 lbs./psf. Adding wind clamps may increase that capacity to -60 lbs./psf or more. Similar to other metal panel roofs, you would want wind clamps in zones
II & III. Many of these type remedies are also allowable for FM insured under their loss prevention data sheet #1-31 2.2.2.2 B for use of External Seam Clamps (ESC).
Once again this will probably not get you to the current requirements in high-wind coastal areas, but you might be close in the Midwest and West. A local engineer can easily check this if you wish.
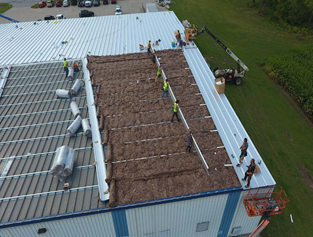 |
Figure 6: Screw-Down Panel Retrofit |
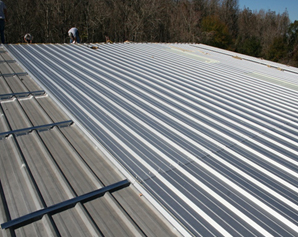 |
Figure 7: Standing Seam Retrofit |
No doubt a new full, code-compliant, roof retrofit is the best way to “harden” your existing building to meet the current wind and/or snow load requirements. It will also provide a dependable, energy-efficient, 60-year or more life roof making
this the lowest life-cycle cost roof system available.
We at Roof Hugger look forward to working with you when you are ready for that new roof. In the meantime, it is great to know you can do a few things to measurably strengthen the roof you have and do it on a limited budget.