Metal Buildings: Sustainable And Adaptable – Part I
By Marge O'Connor, DesignandBuildwithMetal.com
Editor's Note: Metal Buildings: Sustainable And Adaptable is a three-part article based on extensive interviews with industry executives representing leading makers of metal building systems. To read Part II – Taking It One Step Further, click here. To read Part III – What Owners And Builders Look For In Metal Buildings, click here.
Part I – Relationships and Technology Solidify the Base
Pre-engineered metal buildings were sustainable before that was trendy. Their efficient use of resources has offered a multitude of benefits for builders, owners – and the environment – for more than 50 years.
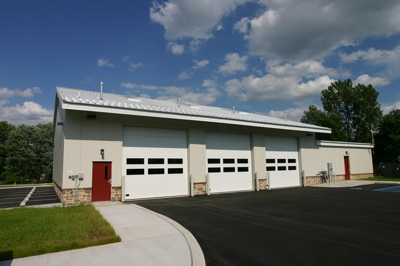 | |
The clear span advantages of metal building systems aren't limited to larger buildings. In Newark, DE, a metal building system from Star Building Systems was
chosen to economically meet the clear span requirements for the 8,000 sq. ft. Glasgow Fire Station. The building is finished with a variety of products, including metal roofing, metal wall panels, stone and EIFS. | |  |
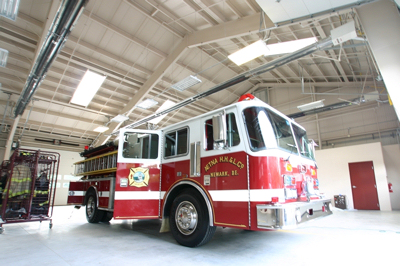 | |
| |
At the core of their success is adaptability. The buildings can be constructed in a variety of shapes and sizes to fit different low-rise applications including manufacturing, distribution, retail, commercial, education, recreation, self-storage, religious,
healthcare and correctional. The wide range of colors for metal roof and wall panels and the ability to combine metal buildings with other building materials creates unlimited design possibilities.
What has kept this market viable over the long term is the ability to make continuous improvements through a combination of technology and grassroots market intelligence.
Although some of the basics about the structural design of metal buildings have not changed a lot, technology has made it more efficient to create buildings to meet performance requirements. In today’s market, computerized design ensures that each
building uses only the exact amount of material needed to meet local codes and the owners’ needs. The process for engineering each structure is a team effort of builder, architect and manufacturer that ensures the structural design meets customers’
specifications.
|  | 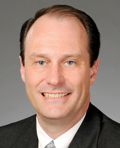  |  | 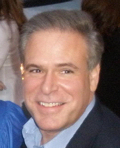 |  | 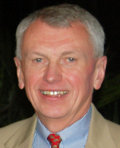 |
|
| Bob Zabcik | | Kevin Mickey | | Phil Symes |
About 90 percent of metal building manufacturers distribute through a network of contractors serving local market needs. If something is not working well, these builders work with manufacturers’ research and development teams to make improvements
and to generate more applications.
“Our partnerships with design build contractors have been a key to expanding the use of metal buildings and meeting the needs of customers in any market or situation. These local contractors can also bring an existing building up to today’s
standards at minimal cost by using the building’s engineering record. This means older buildings such as those built in the 1950s or 1960s with one or two inches of insulation can be updated by re-roofing, adding insulation and sometimes cool
coatings. A brick or masonry structure would require a variety of contractors rather than a single source to do this,” says Philip M. Symes, Vice President, Sales & Marketing, for Star Building Systems, Oklahoma City, OK.
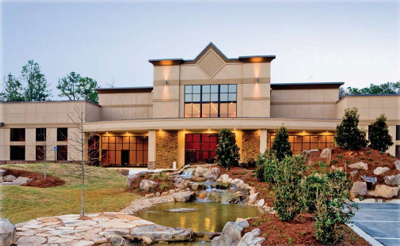 | |
You can't judge a book by its cover and you can't always recognize a metal building from its appearance. Shown above is the 35,000 sq. ft. Harvest Church in Byron, GA.Constructed using a metal building system from Nucor Building Systems, the exterior is finished with an exterior insulation
and finish system and features parapet walls to hide its roof line. Click image to enlarge. | | |
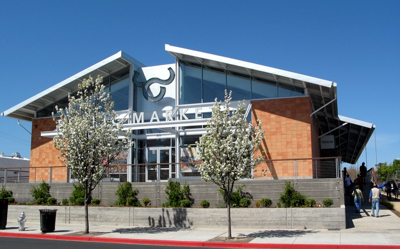 |
|
Elements of metal building construction can be detected on the exterior of the Oxbow Public Market in Napa, CA (shown above) but it is on the inside where the method of construction becomes unmistakeable. There, exposed framing plays a
key role in achieving the project's industrial aesthetic goals. The building system was provided by Metallic Building Co. Click
images above and below to enlarge. | | |
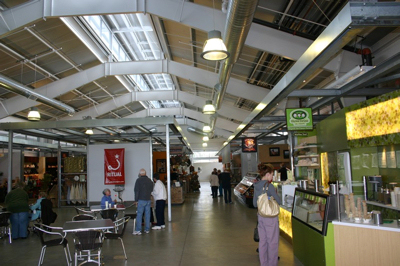 | |
This method has additional benefits, says Wes Brooker, Marketing Development Manager for American Buildings Company, Eufaula, AL. “There is less inherent risk for an architect or specifier working with a metal building manufacturer because responsibility
for meeting local building codes, execution of unique designs and overall building performance becomes a team effort.”
Brooker also notes that metal building manufacturers use their experience with a wide range of similar buildings to ensure design performance. He estimates that manufacturers sell more than 2,000 buildings a year, so they can draw upon this wealth of
information from erected buildings to make design improvements.
“As metal building manufacturers, we control the entire shell. We look at it as a whole system with wall panels and roofs, so we know how to adjust the framing for all conditions. One of the reasons metal buildings stand up very well in seismic,
hurricane or other conditions is because we look at the affect on the total structure when engineering it. Other types of structures are put together in multiple parts - it’s not necessarily a better or worse way - it’s just different,”
Brooker says.
This steady flow of development has been accelerated by significant changes in technology, which has expanded opportunities in several areas.
According to Jim Peckham, Manager of Marketing, Varco Pruden Buildings, Memphis, TN, architects have used metal buildings in new applications in the last 20 years. “They’ve stepped away from thinking of metal buildings as just boxes. Schools
and churches could be considered one of the biggest turnaround markets for our industry. Schools were typically brick buildings; now we see pre-engineered metal buildings designed to function as long-term solutions.”
|  | 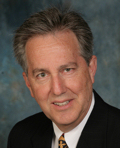 |
| 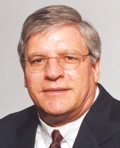 |
| | Roger Burlingame | | Wes Brooker |
Kevin Mickey, Division Sales Manager, Nucor Building Systems, Terrell, TX, identifies more recent changes. “Although we are always tweaking our products, the biggest changes have been in how they can be used in different applications. Architecturally
complex projects have typically not been the mainstay in our industry but that’s changing because of advances in engineering and architectural technology. These improvements will continue to change the way our industry works and allow us to
be more competitive on complex architectural projects. BIM (Building Information Modeling) lets us take complex ideas and integrate those with aesthetics as we’ve never done before. It will change our industry as much as AutoCAD did before and
allow us to design much faster and to increase the quality of the design.”
Changes in manufacturing aren’t always as dramatic, but more of a continuous improvement process. “Manufacturers of metal buildings are always tweaking their systems to move in the direction of where they want to be in 20 years. An example
of this can be found in traditional fiberglass systems such as standoff fasteners that hold the panel an inch or more from the framing. This mitigates the compression of the fiberglass batt at this location and improves overall R-Value,” says
Bob Zabcik, Director of Research and Development for NCI, on behalf of Metallic Building Company, Houston, TX.
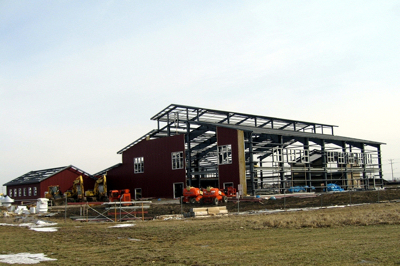 | |
No matter the style, metal building systems can be used to achieve the look. In the case of the Stephen D. Persinger Recreational Center in Geneva, IL, the intent was to make a new 50,000 sq. ft. rec center look like a big barn. But at
the heart of the building's construction was a metal building system from Varco Pruden Buildings.
Click to enlarge. | | |
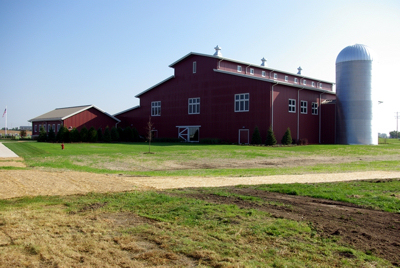 | |
| |
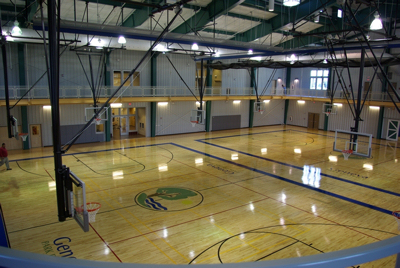 | |
While the market can’t be controlled, manufacturers have adjusted to economic conditions by engineering their products to fit new markets and code requirements.
“The flexibility of metal building systems allows the industry to adapt quickly to conditions. During the recession of 2001-03 many companies learned how to engineer and manufacture school buildings. Last year, the greatest construction crash in
our lifetime, our industry almost doubled its involvement in government construction from 15 percent to 28 percent,” says Brooker.
In the last 10 years, the drive toward improving building performance and better use of resources has been a major factor. Because metal building manufacturers deal with the entire structure, they are most prepared to deal with these changes.
“We design for what’s required based on municipal codes, which can affect several areas, including energy, lighting, and load requirements. Depending on building requirements we may have to change our structural design to fit the insulation
system either for depth of columns or bracing. Today’s codes can also dictate aesthetics, and some municipalities do not allow metal wall panels. In those cases we’ve had to create details of how to use other materials for exterior facades,”
says Mickey.
Advances in technology have been a benefit in dealing with new building codes, which have primarily been government mandated. “Energy efficiency is a significant influence in the changes in our industry and we have to accommodate it to stay competitive.
Another example is electronic systems which allow us to custom design and engineer buildings faster and make them more efficient with less material waste,” notes Zabcik.
The emphasis on preserving resources has brought other changes. Manufacturers have turned to digital communications while maintaining personal contact with customers in other ways, such as in-person education sessions. Several companies also have green
or LEED experts available to assist builders and architects.
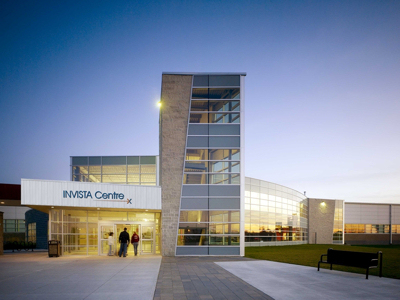 | |
For their sustainable and energy efficient qualities, metal building systems and components are frequently selected for projects targeted for LEED certification. The INVISTA Centre in Kingston, Ontario, Canada, was designed in accordance
with LEED Gold standards. In addition to being made from recycled materials and being recyclable, its metal wall and roof panels feature cool coatings. This project's metal building manufacturer was American Buildings Co. Click images to enlarge. | |  |
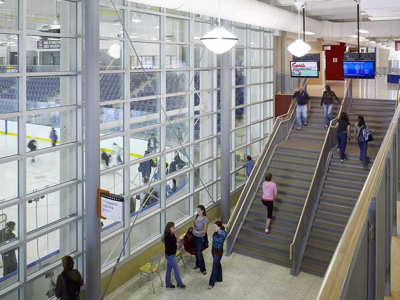
| |
“The building-construction market has become more focused on the benefits of energy efficiency and that makes us think more about how we address those issues in both our manufacturing process and in the final products. We’re very attuned to
what we show on our Web site, especially regarding green and LEED. But architects say they still want hard copy documents so we continue to publish details and charts in our product brochures,” says Roger Burlingame, President, Ceco Building
Systems, Columbus, MS.
Electronics has also changed how companies market to and educate the different audiences. “We produce and host a lot of Webinars but the biggest change is to have all of our specification brochures and engineering manuals readily available online.
Now we can direct designers to the Web site for instant access to details. All drawings for thousands of details are also online so a customer or architect can go to our Web site to find what they’re looking for. It’s changed how we talk
about our products with architects and builders,” says Mickey.
Zabcik agrees: “It’s our job to educate the consumer about what we can provide for their buildings. We reach out to end users with white papers and cost studies. We also hold sessions at our builder meetings to educate builders on what’s
ahead and how to address the end user’s concerns.”
Peckham offers a good comparison on the value of different technologies and communications. “The impact of the computer and the Internet on the metal building industry is amazing. Computerization has sped up the manufacturers’ estimating process,
but due diligence in information gathering is still a key part of the decision process and still takes time to do right,” he says.
Burlingame sees the continuing education courses his company holds with architects as a great face-to-face opportunity to learn what’s most important to them. “We talk about energy efficiency and metal buildings in general. After the presentation,
there is an informal session that gives us a chance to provide more specific information and answer questions. Although we plan to offer online education such as Webinars in the future, we believe online misses a bit of the interactivity that you
can only achieve when you meet in person.”
As electronic technology was changing communication and manufacturing, other materials and processes were making significant transformations that added to the efficiencies offered by metal buildings. The second part of this series covers the specifics
of how these are now being integrated into metal buildings.
Editor's Note: Our second installment, Taking It One Step Further, will discuss changes in metal building designs to keep pace with continually evolving energy codes.
For hotlinks to the websites of the companies mentioned in this article, as well as dozens of other leading manufacturers of metal building systems, please visit the Metal Building Systems and Components section of our Manufacturers & Suppliers Directory here.