By Marge O'Connor, DesignandBuildwithMetal.com
Editor's Note: Metal Buildings: Sustainable And Adaptable is a three-part article based on extensive interviews with industry executives representing leading makers of metal building systems. To read Part I – Relationships And Technology Solidify The Base, click here. To read Part III – What Owners And Builders Look For In Metal Buildings, click here.
Taking It One Step Further
In the last 10 to 15 years, significant changes have enhanced the ability of metal buildings to meet new energy standards. These improvements in roofing, insulation, coatings, and solar systems have also created more opportunity in the green building
market for these resilient structures.
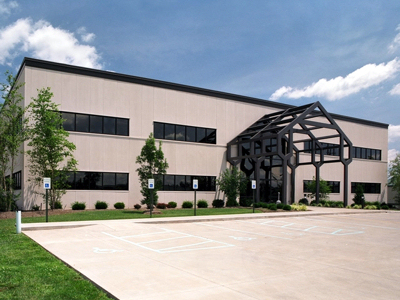 | |
| |
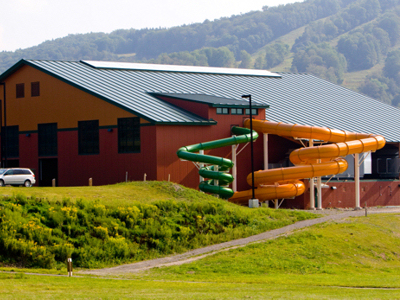
| |
Insulated metal panel systems are widely used in metal building construction. In the example at the top, insulated metal wall panels from Insulated Panel Systems were used to wrap the walls of the WS Construction headquarters in Versailles,
Kentucky. The building was built using a metal building system from Metallic Building Co. Right
below it is the Hope Lake Lodge Indoor Water Park in Cortland, NY. Constructed with a metal building system from Varco Pruden,
the pool enslosure area is clad with insulated metal wall and roof panels from Metl-Span.
Click images to enlarge. | |
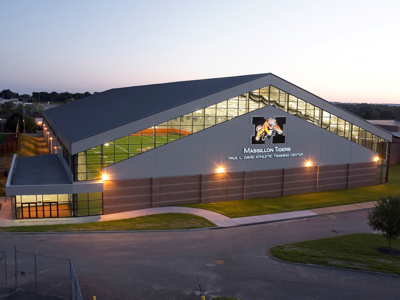
| |
One of the many benefits of incorporating insulated panel systems with metal buildings is that the liner side of the sandwich panel doubles as an interior finish. You can see this in the side and endwalls of the Paul L. David Athletic
Training Center in Massillon, OH. The building was constructed with a Varco Pruden metal
building system. The insulated wall panels were manufactured by Metl-Span.
Click images to enlarge. | |
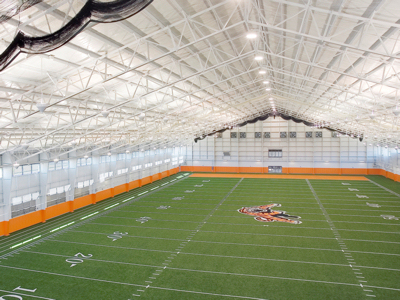
| |
“Metal buildings have been designed to optimize strength and material so they’ve always been efficient, but the introduction of cool coatings and different insulation options made significant changes in the market from where we were 20
years ago,” notes Jim Peckham, Manager of Marketing, Varco Pruden Buildings, Memphis, TN.
Adding standing seam roofs on metal buildings also helped spur developments.
“Standing seam roofs allow the insulation to sit between the panel and the framing, increasing its effective R-Value and improving system performance. Fiberglass and roll insulation in two- to four-inch thicknesses had been the primary insulation.
As energy became more expensive, buildings began to need better performing envelopes. The standing seam roof allowed us to increase insulation thicknesses because there was more space available and the insulation systems grew to meet this new
market demand,” says Bob Zabcik, Director of Research and Development for NCI, on behalf of Metallic Building Company, Houston.
This drove changes in panels and insulation systems to make them more efficient.
“As codes became stricter about insulation, fiberglass couldn’t grow any further so suppliers began to create hybrid systems that functioned better than fiberglass alone. Today, hybrid insulation systems are used to meet more stringent
building codes. Beyond these are the insulated metal panels (IMPs), which are now top of the line for insulation performance,” adds Zabcik.
But the influence of sources beyond the customer is now creating a greater challenge in product development. “The biggest issue for our industry is how ASHRAE affects the way we specify insulation. The way we used to specify small amounts of
insulation over purlins and girts won’t work today in many municipalities. Although ASHRAE is not a code body, its guidelines impact how we design and its recommendations are being incorporated into the energy design of the entire building.
The belief is that these requirements will continue to become more stringent and continue to impact construction design for the foreseeable future,“ says Kevin Mickey, Division Sales Manager, Nucor Building Systems, Terrell, TX.
Several manufacturers have turned to IMPs for both roof and wall applications as a way to meet these changing standards over the long term. In the last ten years new foam systems have further enhanced the performance of IMPs and increased their use
on metal buildings.
|  | 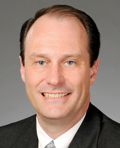
|  | 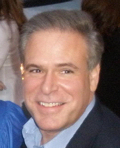
|  | 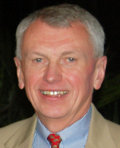
|
| | Bob Zabcik | | Kevin Mickey | | Phil Symes |
“We’ve moved from basic attempts at achieving energy efficiency to a much higher level of efficiency through the integration of energy saving technology into products. Single skin panels combined with varying amounts of blanket insulation
are not always the best solution. Today we have cost-efficient, foamed-in-place panels that offer high R-value efficiency with an approximate R-value of 7.1 per inch of product. This means a 3-inch foam insulated metal panel would have an R-value
of 21. The foamed-in-place panel concept provides other benefits. Because the insulation is sandwiched between two metal panels, the insulation and panel go on in one step and the building now can have a great look on both the interior and exterior,”
says Roger Burlingame, President, Ceco Building Systems, Columbus MS.
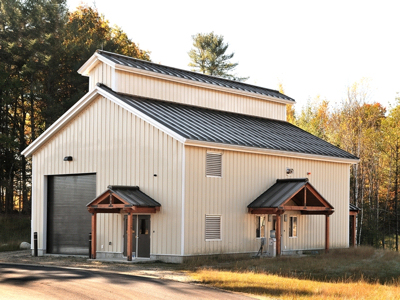 | |
Metal building systems are frequently used for buildings designed with LEED certification in mind. Shown above is one of the three buildings that comprise the White Mountain Administrative Complex in Campton, NH. It was designed to
resemble a New England sugar house. It was built using a metal building system and claddings from Star Building Systems.
Another three-building LEED-certified project was in the town of Greensburg, KS. There, Liberty Building Systems manufactured the metal buildng systems and components needed to construct a new transportation building, a noxious
weed building and a recycling center. Click images to enlarge. | |
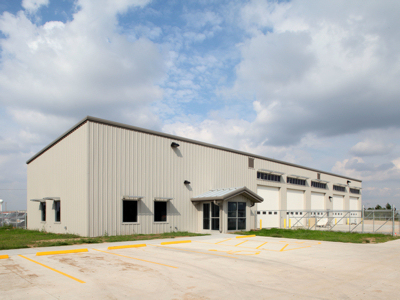 | |
This trend is taking hold as more manufacturers and buildings owners discover the value of IMPs for different applications.
“The IMPs are definitely utilized more in the commercial-industrial market for walls and in the last two years, more for standing seam roof panels. These panels are usually 24 gauge on the exterior and 26 on the interior so there is very little
weight impact to using IMPs on the roof,” adds Mickey.
Perhaps the most visible change over the last ten years was in coatings for metal panels. More colors were developed and cool coatings became a byword of energy efficiency. But the term and the use of the coatings are often misunderstood.
Burlingame notes the options offered by cool coatings. “We have advanced our thinking from just the aesthetic elements of our panels and coatings to being more conscious of the interaction of the paint finish with the environment. For example,
in the south we think about energy savings in the summer so we want cool coatings. But in the north in the winter you want something that saves the heat and brings it into the building to reduce heating costs. So a cool coating or energy saving
paint that would be useful in the south might not be the best choice in the north.”
Using cool coatings wisely is also a major concern for Zabcik, who shares his insight on the critical steps in the process. “We need to be realistic about cool roofs. They are chosen for energy reasons or environmental reasons. These are two
distinct and different needs that should not be confused. Using a cool roof to mitigate a heat island should occur only where heat island is a problem; using a cool roof in a cold climate doesn’t make sense when heat island is not an issue.
It could actually make a building less energy efficient,” he cautions.
|  | 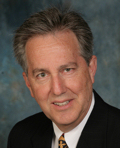
|  | 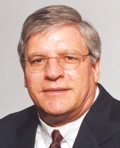
|
| | Roger Burlingame | | Wes Brooker |
He continues: “To increase energy efficiency with a cool roof, you need to determine whether the building will need more energy for heating or cooling over the course of a typical year. If more energy is used to cool the building, then a cool
roof is a good solution. But if efficiency in heating is more of a concern, then you want the roof to absorb the heat energy. The best way to know this is to run a modeling program to find out whether a cool roof is a viable option.”
Another more recent change in roof options for metal buildings is the use of solar systems. Because of metal roofing’s long life span, it is considered the best option for integration with solar systems. But how this market will develop is still
to be determined.
“The use of solar panels is increasing. They are being integrated into the roof systems of metal buildings to serve both a design and functional purpose, which impacts the design from load and attachment standpoints. We see that business changing
rapidly and are responding to those requirements,” says Mickey.
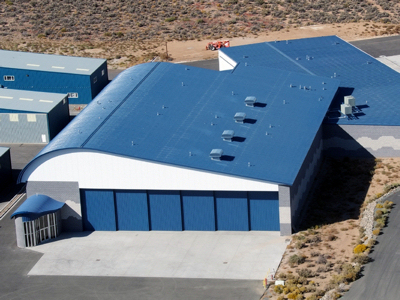 | |
Cool coating technology was developed in the early 1990s and is now offered as a standard paint finish by some metal building and component manufacturers. From an appearance standpoint,paint finishes based on cool pigment technology
look just like any other paint. Shown above is the main hangar at the Jet Ranch in Carson City, NV. The hangar was constructed with a metal building system by American Buildings Co. The cool color-finished metal roof panels, also by American, were curved to specification by Curveline
Inc. Click image to enlarge. | |
Peckham agrees on the market impact. “The use of solar energy systems is growing in some markets. As buyers see the big picture solution going forward, there will be a lot more applications for solar in our industry.”
Builders who want to get involved in installing solar, will want to learn more about the systems. “When choosing a solar technology, it is important to look at the service life of the roof and the PV equipment as well as the cost per watt of
the installed system. If the equipment outlives the roof, a significant cost is involved in removing and replacing the equipment when the roof fails. In the case of metal roofing, where the roof is likely to outlive the equipment, this cost
is avoided,” adds Zabcik.
While the desire and the market seem to be on the rise, there is still concern for the timing. “Right now the solar industry is economically upside down; it costs more to produce products than they typically sell for. However, most producers
have the patience and the resources to wait out the market because they know it’s going to become more significant in the next five years, especially as more states and local utilities consider incentive programs,” says Zabcik.
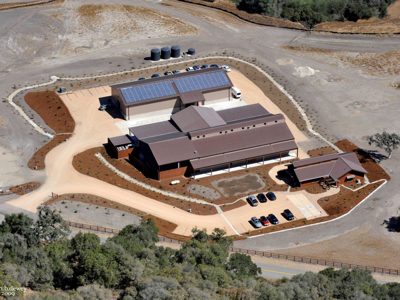 | |
Rooftop solar is the latest trend in metal building design. The Foxen Winery in Santa Barbara County, CA, exemplifies this trend. Constructed with metal building systems by Varco Pruden, insulated metal wall panels from Kingspan Insulated Panels and metal roofing by Morin, a Kingspan Company, the three-building winery complex also incorporates rooftop-mounted crystalline solar panels. Click
images to enlarge. |  |
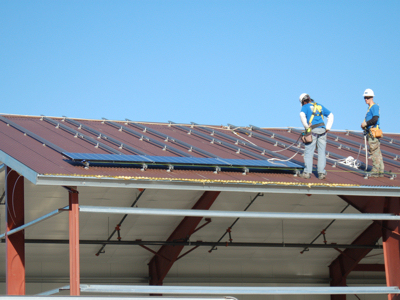 | |
The awareness of metal’s benefit as a recyclable material with recycled content has also grown in the last ten years. This has been another selling point for metal buildings and a reason for manufacturers to tell a realistic green story
to end use customers.
“Everyone realizes they need to show some competence and compliance with green building practices and sustainable applications. But metal buildings have always been a green choice because of the recycled content of steel, and the engineering
benefits that make the most efficient use of this natural resource. Steel as a material has been consistent and has always been one of the most sustainable, resusable materials. It’s just become more recognized in the market place as
a green material,” says Peckham.
For metal buildings, sustainability and recycling are nothing new, but the terms have achieved new meaning. “The green building movement has created a lot of good ideas and opportunities. For one, it’s increased awareness of steel’s
recyclability and its green attributes. But sustainability is about creating a resource-efficient building. Structures built today may have a lifecycle of 30 or 40 years and can be updated later to get another 30 or 40 years out of them. So,
when a location wears out because of changes in real estate, we can take down the building and recycle or reuse the materials to keep them out of the landfill and save on natural resources. That’s the value of our structures to the whole
green building movement,” says Symes.
The changes of the last decade have solidified the position of metal buildings as efficient, adaptable structures. To help designers and building owners become more aware of how to use these benefits, manufacturers will continue to offer advice
and improve products. In the next part of this article our experts offer insight on how this can occur.
Editor's Note: Our third installment, What Owners And Builders Look For In Metal Buildings, will discuss building features and options that owners may want to consider when choosing the metal building approach.
For hotlinks to the websites of the companies mentioned in this article, as well as dozens of other leading manufacturers of metal building systems, please visit the Metal Building Systems and Components section of our Manufacturers & Suppliers Directory here.