By Scott Moffatt, PPG
This article is the third in a series of five intended to help architects and other building professionals more effectively color-match architectural metal coatings so that:
1. Building components arrive on the job site coated in the colors specified; and
2. Components produced by different coatings applicators appear as a coordinated whole when installed together on a building.
The first article covered five rules for proper color-matching at the specification phase. The second article identified five steps for how to manage multiple applicators and application methods being used on the same project. This
one details three key variables to manage during the application process.
Batch Manufacturing, Metals and Paint Technology
The coatings process is inherently variable. No quality control program, no matter how stringent or demanding, can account for all the contingencies involved in the coatings process.
In fact, many factors that affect color consistency are beyond the coatings manufacturer’s control. For instance, pigment manufacturers set strict tolerances for the formulation of their products. Yet, these pigments still have ordinary variations
that ultimately are passed on to the coatings applicator.
Similar variability may apply to the micas and metallics. It is difficult to enforce strict tolerances for these products simply because they are based on “natural” raw materials.
Comparatively speaking, the impact of these raw material variations is small. The greatest potential for color-matching problems is found in the three major variables related to the application process, which are:
• Batch variation
• Variation in metal substrates
• Paint technology
Batch Variation
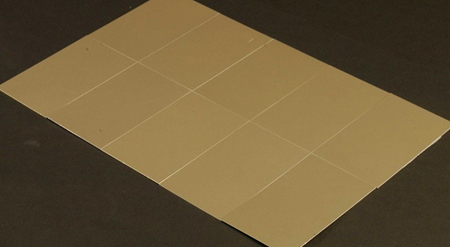 |
These panels illustrate the natural variation inherent in coatings manufacturing. Although the colors appear slightly different, each of these examples is within industry-standard specification tolerances. |
Problems with batch variation arise when coatings are produced by more than one coatings manufacturer or if one coatings manufacturer makes more than one batch of a coating to complete a job.
Typically, variation between batches is minimal and minor differences can be masked through proper application of the product. Nevertheless, there are several steps architects and contractors can take to minimize potential batch variation problems.
1. Determine the amount of coating that will be required up front. That may enable the coatings manufacturer to produce all the coatings in a single batch, eliminating batch-to-batch variation. If a single-batch approach is not possible, the next best
solution is to minimize the number of batches needed.
2. Reduce the number of coatings manufacturers and coatings applicators. Trying to match batches and standards among different coatings manufacturers and coatings applicators is extraordinarily difficult. Raw materials vary from one coatings manufacturer
to another, as do the manufacturing processes, color measuring standards and equipment. When possible, specify all your coatings from a single coatings manufacturer and coatings applicator.
3. Try to get all metal painted at the same time. Again, one batch of paint with a single application run — using the same operator in the same operating conditions — is the most efficient way to eliminate variables.
4. Finally, if additional coatings are needed to complete a job, always specify that the new order matches the original batch number used. This gives the coating manufacturers and coatings applicator a consistent reference to use during production.
Metal Substrates
When coatings are applied to metal, two variables can affect their final appearance. The first is the type of metal used (most commonly steel or aluminum). The second is how the metal was pre-treated. To promote color consistency across all the substrates
used on an individual building, the architect or contractor should:
1. Make the coatings manufacturer(s) aware of all the different metals being coated. This will allow the coatings manufacturer to match colors across the entire range of substrates for a given project; and
2. Verify with the coatings manufacturer(s) that its product has been engineered for use over the desired substrate(s) and that it is compatible with the pretreatment method used by the coatings applicator.
Paint Technology
Coatings are formulated using a variety of base resins and pigments. When coatings are mixed, subtle differences in color and metamers* can be exposed. That is why viewing color samples under actual lighting conditions is vital.
Paint chemistries also can change according to the performance specification required for the coating. The same pigment deposited in a PVDF coating will usually produce a color that looks different from the same pigment in an acrylic coating.
The introduction of powder coatings into the architectural market has added another significant variable to color control, as liquid and powder coatings will never match perfectly, especially in mica and metallic formulas. There are three main reasons
for this:
1. Liquid coatings are much smoother in appearance than powder coatings based on film thickness and because liquid can be reduced with solvent to improve leveling. Powder coatings are never adjusted at the applicator and come ready to spray.
2. Powder coatings also have a minimum paint thickness 2.5 to 3 mils versus a standard thickness of 1 mil for liquid coatings. Because they are applied in greater thicknesses, powder coatings tend to hide or bury the mica and metallic pigment in the paint
film so that it cannot been seen on the finished part.
3. Finally, micas and metallics appear different in liquid and powder coatings because coatings manufacturers are limited in the amount of mica or metallic they can load into a powder coating, as higher volumes will become heavy and settle out in powder
formulations.
For all these reasons, it is essential that architects and contractors communicate to their coatings manufacturer(s) all performance specifications related to a project. If more than one performance specification is required, colors must be matched in
each technology (liquid or powder) and each resin chemistry prior to application.
The fourth article in this series will identify four steps to ensuring proper panel matching during panel installation.